The Digital Engineer's Guide to RF PCB Layout and Routing
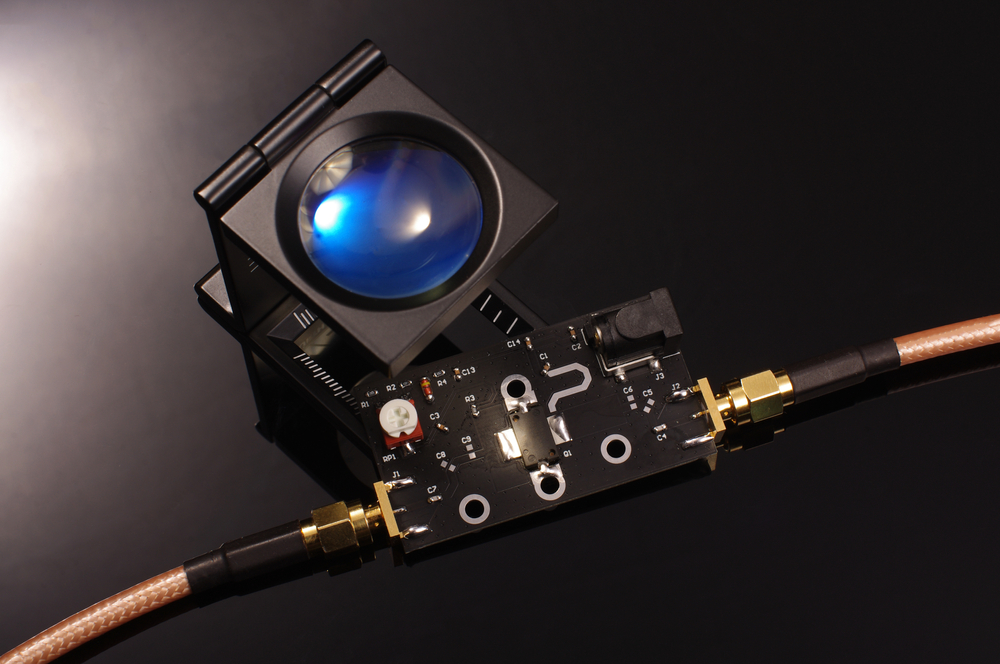
I work with a lot of different folks in the electronics industry, including a few companies on the materials and semiconductor side. During a meeting, one startup founder remarked to me “EE’s only needed to learn RF design to pass their qualifying exams. Now we have to go back and relearn it for the products we’re designing.” Coming from a lasers and optics background, RF design and analog design in general are natural to me, and I always underestimate the difficulty in digital design. Now with modern systems running at higher frequencies, incorporating multiple wireless protocols, and interfacing with many analog sensors, advanced designs require knowledge from both disciplines.
If you’re a digital designer, you’re comfortable working in the time-domain and you probably have a great conceptual understanding of time-dependent electronics behavior. If you’re now starting to work in the RF realm and you need to design an all-analog or mixed-signal system, RF PCB layout will need to become a new specialty. Once you’ve created your RF PCB layout, there are some field solver tools you can use to evaluate your designs and ensure your system will operate as intended. If you’re a digital designer and you’re now jumping into high frequency analog design, keep reading to learn more about RF PCB layout and routing.
Getting Started With RF PCB Layout
When you’re starting an RF PCB layout, there are some considerations that are typical for any board. How large is the board? Where do the critical components or connectors need to be located? How will it mechanically fit to its enclosure? These are all important questions for any PCB, but RF systems carry some unique design considerations that need to be answered.
Here are some of the important questions to answer when developing an RF PCB layout or a digital system with a high frequency RF section:
- What protocols are involved? RF systems will need to do something involving high frequencies, which might be running at some standardized protocol and frequency range. There might also be more than one protocol in the system, and different protocols should not interfere with each other.
- What frequencies are involved? In general, lower frequencies are more forgiving than higher frequencies because parasitics are less noticeable at lower frequencies. RF systems are also less likely to couple radiated noise to each other at lower frequencies.
- What digital interfaces are involved? For some systems, the digital interfaces will be slow (SPI, I2C, etc.) and will not have a major effect on analog performance unless you ignore most best practices for routing. Embedded systems with high compute power will use high speed protocols like gigabit Ethernet, DDR, PCIe, and others.
Obviously, the term “high frequency” is subjective, but the important point is that the frequency will affect many design decisions in an RF PCB layout. Then there are system-specific requirements, such as you might see in a radar PCB or a system with MIMO antennas. The analog and digital sections need to be treated differently due to the way analog components interact with RF signals. This will then influence your component placement and routing choices in the layout.
Mixed-Signal PCB Floorplanning
Digital designers should approach an RF system with a floorplanning approach. The high-level goal here is to group components into functional blocks based on their role in providing functionality to the product. A side goal is to eliminate a situation where you need to route long RF interconnects all over the board to make the required connections. Myself and my team will do this in the schematics just to keep things simple once we import into the PCB layout, and doing this on the front end helps you keep things organized.
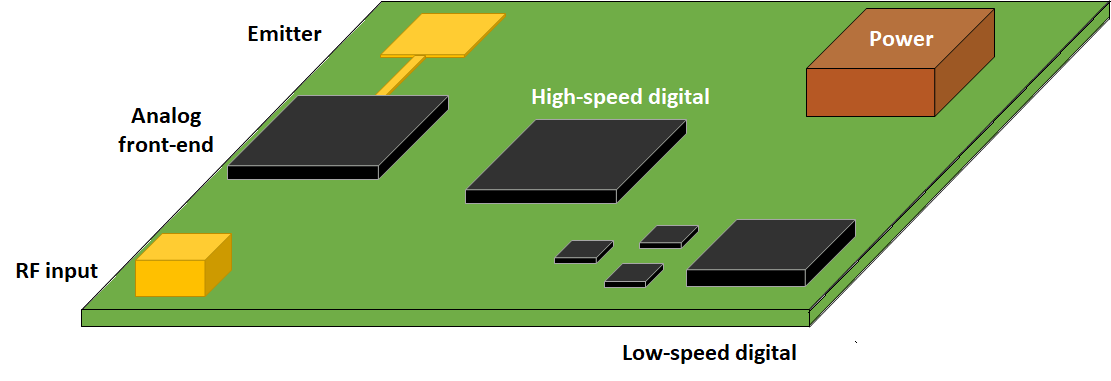
Try to keep things compact and segment things into different blocks where possible. When you start breaking up your functional blocks, you’re at risk of needing to route RF and digital traces back-and-forth across the board. This then creates more spots where strong crosstalk can occur, and it becomes more difficult to track your return path throughout the board. Floorplanning needs to be done alongside another important task: designing the PCB stackup.
PCB Stackup Design for RF Devices
The stackup design is related to floorplanning in that your routing strategy and layout will require a grounding strategy, especially at practical RF frequencies. The PCB stackup you use will determine your power and ground access in the PCB layout, as well as available space for routing signals in your board. An example of an 8-layer count PCB stackup you can use for an RF design is shown below. Although this is not typical, it provides the pattern for selecting layers and arranging signal vs. plane layers in the stackup for low-speed, high-speed, and RF signals.
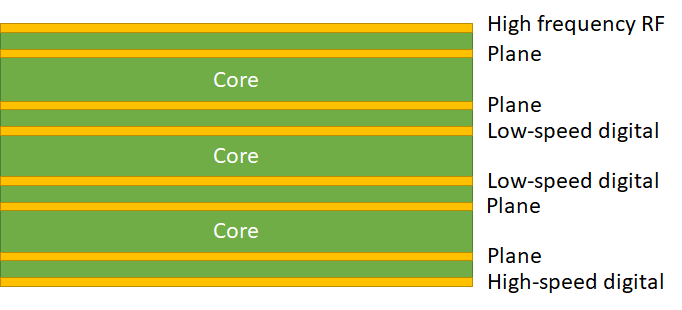
In this example stackup, there are traces on the top surface layer to provide direct connections between high frequency analog components; these could be routed in any of the routing styles I’ll present below. Directly below this, we have ground/power planes, which are adjacent to provide interplane capacitance and to ensure stable power is delivered throughout the system (both for digital and analog components). In the internal layers, we can have other (lower frequency) RF signals, or we can have low-speed digital signals. On the bottom surface, I’ve allowed for the possibility of high-speed digital signals, although we could have these various signals mixed across the top and bottom layers as long as the return paths are controlled.
Read more about planning your PCB stackup for mixed signal systems and tracing a return path in a recent article from Kella Knack.
If you’re not packing a lot of digital components on the board, you can probably give up 2 layers I would argue you’ll need at least 4 or 6 layers with small component counts due to the need for grounding in the system. The goal in grounding is to support routing, which I’ll discuss in the next section.
Plan Grounding to Support Routing
Grounding is important for defining a return path in an RF layout, although it’s better to think in terms of the space in the board occupied by traveling electromagnetic waves surrounding a trace. Note that the signal traveling on an interconnect does not appear as flowing current on a conductor; this is a conceptual model that doesn’t match reality. The truth is that the electromagnetic field occupies some space around the conductor, and the strength of the field within this space will be determined by the presence of conductors around the interconnect.
The field around the trace then causes a return current to appear as a displacement current. This is because, if we look at the microstrip trace and ground plane arrangement shown below, we have two conductors brought to different potentials that are separated by an insulator (the PCB laminate material), forming a capacitor. The displacement current in the ground plane follows the electric field lines as they terminate at the ground plane.
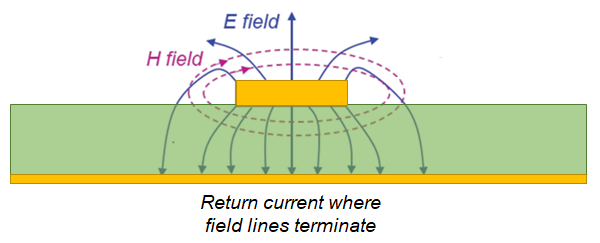
Why is this all so important for RF PCB layout? The reason is that placing ground near your high frequency interconnects confines the field around the interconnect, and it ensures the return current stays closer to the trace at higher frequencies. Without the ground plane near a trace, we don’t know exactly where the return current will be, creating strong emission and reception of EMI.
To quickly summarize this point on grounding, we have two guidelines:
- Don’t physically separate or split a plane layer into islands with digital and analog components and try to tie them together with a capacitor. You’ll have a poorly conceived return path that creates an EMI problem. Just use a single plane layer and learn to trace return paths.
- Take advantage of plane layers to ensure signal and power integrity. This means that, even if you have a simple RF board with only a few components, you’ll need at least a 4-layer board to provide the necessary plane layers.
To learn more about the importance of grounding in an RF PCB layout, read more about return paths in your PCB in this recent article.
Routing Your RF Traces
Now it’s time for the fun part: RF routing. All RF routing requires controlled impedance. This could require placing a termination network to ensure power transfer into a component (e.g., a divider or antenna), or placing a filter/amplifier to adjust specific frequencies traveling along an interconnect. Components that have an integrated RF output might have the required termination on-die, so be sure to check for this before placing any termination components at the driver end of your RF interconnect.
Trace Geometries
Once it’s time to route your critical RF traces, you’ll need to decide on a trace geometry. At Wifi frequencies and higher, most component application notes will recommend using a grounded coplanar waveguide to route your RF traces. However, it’s up to you as a designer to weight the pros and cons of different trace geometries. I’ve summarized these in the table below.
|
|
|
|
|
|
|
|
|
|
In all of the above geometries, we’re generally dealing with narrowband signals, and FR4 laminates tend to have quite low dispersion within narrow bandwidths you’d find in practical wireless/RF signaling standards. The one exception I can think of at the moment is software-defined radio, which requires the same approach to designing to a target impedance as traces for digital traces (i.e., a wideband approach). Aside from this application area, you can generally ignore FR4 dispersion and you’ll get an accurate impedance calculation with a field solver as long as you know the Dk and loss tangent values at your target frequency.
The Impact of Trace Length and Vias
I bring up trace length and vias on RF interconnects because they can have similar effects on the total loss and signal distortion in an RF PCB, but not in the same way. Some designers will state that you should always use the shortest possible trace lengths on high frequency signals, but they don’t seem to quite understand why it’s important. Loss is a factor, but so is input impedance, which is particularly important in termination networks and interconnects with coupling capacitors.
In short, there is a short list of guidelines to follow regarding trace lengths and via counts on interconnects:
Traces between components in RF circuits, such as passives in a filter, can behave as transmission lines, even if routing between traces is short.
- Losses are important, but losses on short interconnects are dominated by return loss, which is due to mismatch between two impedances. The mismatch needs to be dealt with designing to accurate impedance, normally with a field solver.
- If you designed a microstrip with controlled impedance, then route it as a microstrip. Don’t route a microstrip as a coplanar waveguide because placing ground pour and vias around a microstrip will modify its impedance.
- Vias can start to act like filters or resonators at high frequencies, such through-hole vias as at mmWave frequencies. Don’t route through too many vias as losses will add up, and don’t leave via stubs on high frequency transmission lines.
- Follow other standard routing guidelines for high-speed/high-frequency PCBs to ensure you’re maintaining impedance and minimizing losses/distortion. I’ll discuss routing more in a future article.
RF PCB layout can be complex for digital designers, but the design features in Altium Designer® will help you route with high accuracy and export your design for analysis in Ansys field solvers with the EDB Exporter utility. Altium Designer and Ansys have come together to give RF engineers and PCB designers an easy way to collaborate on high frequency designs and fully evaluate an RF PCB layout.
When you’ve finished your design, and you want to release files to your manufacturer, the Altium 365™ platform makes it easy to collaborate and share your projects. Features like commenting, design sharing, and user access management allow you to easily move your RF PCB layout through a PCB design review, where required changes can be tagged in the PCB layout and sent back to a designer for modification. Altium 365 also makes it easy to quickly share your fabrication data with your PCB manufacturer, and all without sending emails or using external chat programs.
We have only scratched the surface of what is possible to do with Altium Designer on Altium 365. You can check the product page for a more in-depth feature description or one of the On-Demand Webinars.