All About PCB Loss Tangent: What it Means and When it Matters
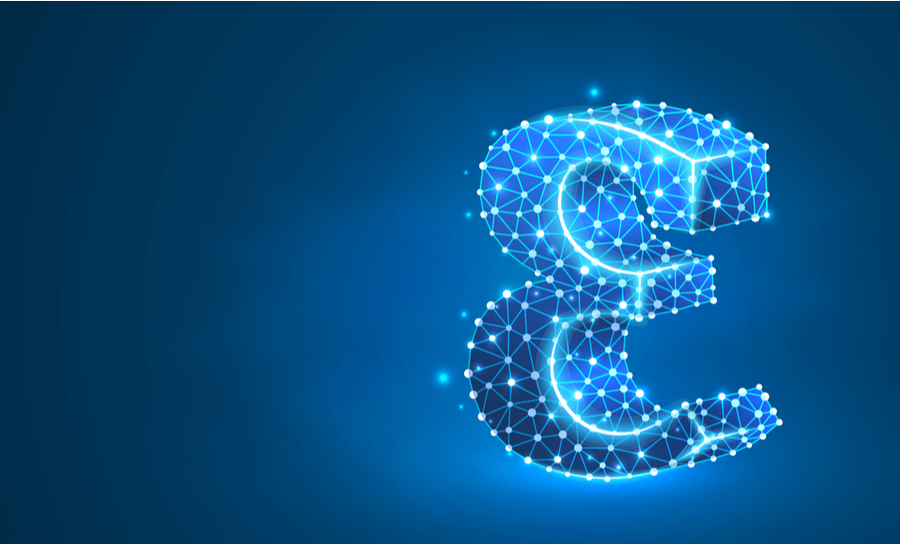
Losses in a PCB interconnect come in many forms. These include dielectric losses due to the PCB substrate and losses on conductors, both of which combine in a unique way to determine interconnect impedance. These terms are also complex functions of frequency, reflecting the nature of dispersion in a real PCB. When we look at the PCB substrate and the conductors, we can divide up our losses into two categories and focus on each during the design.
Of the two categories of losses in your interconnects, a PCB’s loss tangent will dominate dielectric losses in commercially available insulating laminates. When including loss tangent values in models for transfer functions, S-parameters, or impedance, you’ll need to use the right set of equations to work with PCB loss tangents correctly. Here’s why the loss tangent matters and what it affects in your PCB.
Equations for PCB Loss Tangent
PCB loss tangent values incorporate a few possible contributions at typical frequencies used in the industry:
- Polarization and relaxation. This arises due to excitation and oscillation of bound electrical charges in the atoms that make up the substrate materials. Whenever a field propagates along a trace, it excites the atoms in the substrate and causes these oscillations.
- Stray conductance in the substrate. Every material has some electrical conductivity, even if it is extremely small (in the case of insulators). For PCB substrates, the value is ~10-11 S/m, so conductivity is normally ignored for commercially available PCB substrates.
- Fiber weave effects. Cavities in the glass-weave of a PCB laminate will produce low-Q resonances and anti-resonances, where certain frequencies will experience constructive or destructive interference. This increases losses as electromagnetic waves travel over the PCB laminate.
Other effects like scattering will become prominent as we start to move into the high-GHz regime and, eventually, into the THz regime, where alternative materials will be demanded. Conductor losses are composed of DC losses (IR drop) and AC losses (skin effect and copper roughness), although copper roughness does have an effect on the dielectric losses, which will be discussed below.
PCB loss tangent values are derived from the substrate’s dielectric constant. If you look through most engineering texts, the definition of a dielectric constant (Dk value) has a pesky negative sign, and it’s still a mystery to me why this is present in the electrical engineer’s version of Dk. It seems that electrical engineers prefer time to run backwards in complex exponentials. I’ve provided the correct definitions for the dielectric constant and loss tangent below.
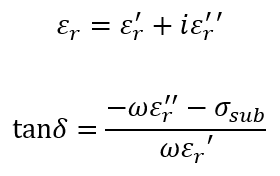
Modeling and Controlling System Losses
Once it’s time to model interconnect losses at different frequencies in your signal bandwidth, you need to know the propagation constant for your transmission lines. Here, we can take a couple of equations from Pozar’s Microwave Engineering textbook. If we take the propagation constant on the transmission line to be γ = α + iꞵ, we can derive the following equations for the propagation constant:
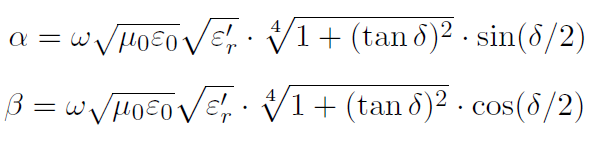
We now know everything related to dielectric losses in the transmission line! To include conductor losses, simply calculate an attenuation constant for conductor losses and add it into the α term above.
As a designer, you only have two levers you can pull to reduce losses: substrate selection and trace geometry. Selecting a low-loss laminate is a good place to start, but make sure the datasheets are accurate and provide data that matches your signal bandwidth (see below). If losses are a problem in the inner layers, consider microstrip or grounded coplanar waveguide routing. The latter gives high isolation when working with wideband digital/RF signals. The other factors that contribute to dielectric losses and PCB loss tangent can only be solved by laminate manufacturers (see below) and fabricators.
Finally, there is the effect of copper roughness on losses. The basic effect of copper roughness is to increase dielectric losses as well as AC losses. The rough surfaces of copper will decrease the span of the waveguide, making the waveguide appear more lossy than the true PCB loss tangent value would produce. This is shown graphically below; the HRMS value is the root mean square surface roughness on the conductor. A rougher surface effectively confines the field to a smaller volume, thereby increasing losses.
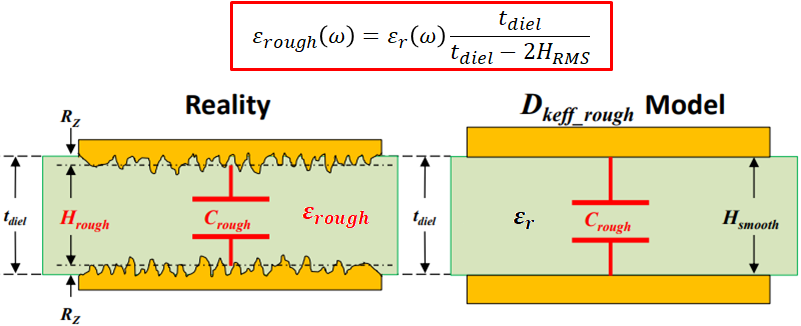
Modeling Dk and PCB Loss Tangent for Laminates
Those in the audience who’ve listened to any of John Coonrod’s podcasts and seminars should know about the asterisk that should be placed next to Dk values in laminate datasheets. First, the Dk and loss tangent values you get from a PCB laminate datasheet depend on the test that was performed to measure them. Different tests with the same laminate under the same conditions can yield different values of Dk and loss tangent.
This occurs because the Dk and loss tangent curves gathered from an experiment depend on the distribution of the electric field in the laminate and the surrounding air/solder mask. This is why microstrips and surface waveguides are described using an “effective” Dk value; the field lines from the trace pass through the solder mask and air above the board before they terminate at the reference plane. Some calculation then needs to be used to infer the real Dk value and loss tangent in the laminate at a specific frequency.
Be sure to take time and understand values and test procedures placed in materials datasheets before you start running simulations from your design. If you can input the right values, you can use the integrated EM field solver in Altium Designer® to develop accurate impedance profiles from PCB loss tangent data. You’ll have a complete set of simulation features and world-class PCB layout utilities to help you design your next PCB.
Altium Designer on Altium 365® delivers an unprecedented amount of integration to the electronics industry until now relegated to the world of software development, allowing designers to work from home and reach unprecedented levels of efficiency.
We have only scratched the surface of what is possible to do with Altium Designer on Altium 365. You can check the product page for a more in-depth feature description or one of the On-Demand Webinars.