What They Don’t Teach You About Fluxes
Introduction
As engineers, we sometimes sit high on our pillowy chairs, looking at the nitty and gritty of the industry — such as the fabrication of the PCB — with a bit of nonchalance. The truth of the matter is, when studied in-depth, PCB fabrication is an extremely complex technological topic that deserves recognition as the most fundamental part of PCB engineering.
Unless connectors, conductive adhesive, wire-bonding, or zebra-tape are used, in the modern electronics industry it’s always necessary to use some kind of flux during the soldering process to create an electric connection.
In this article, we’ll discuss fluxes — what they are, what they are made of (yes, there is going to be a lot of chemistry, don’t be scared), how they should be used, and in what direction the industry is going.
History
Choosing the right kind of flux is something where the interests of the electronics manufacturing services (EMS) house and of the customer (that’s you) can experience a divergence of values. The EMS house wants the cheapest and easiest to use base materials, with the highest yields possible. The customer, however, will likely want to take into consideration future reliability, corrosion resistance, environmental impacts, and compatibility with successive treatments, such as conformal coating.
Up to the 70s, most fluxes were rosin-based. Rosin is a resin obtained by heating and/or distilling of naturally-occurring resins, such as those produced by pines and other conifer trees. It has been used for millennia to increase frictions (for example in violin bows), as glue, binding agents, or varnish.
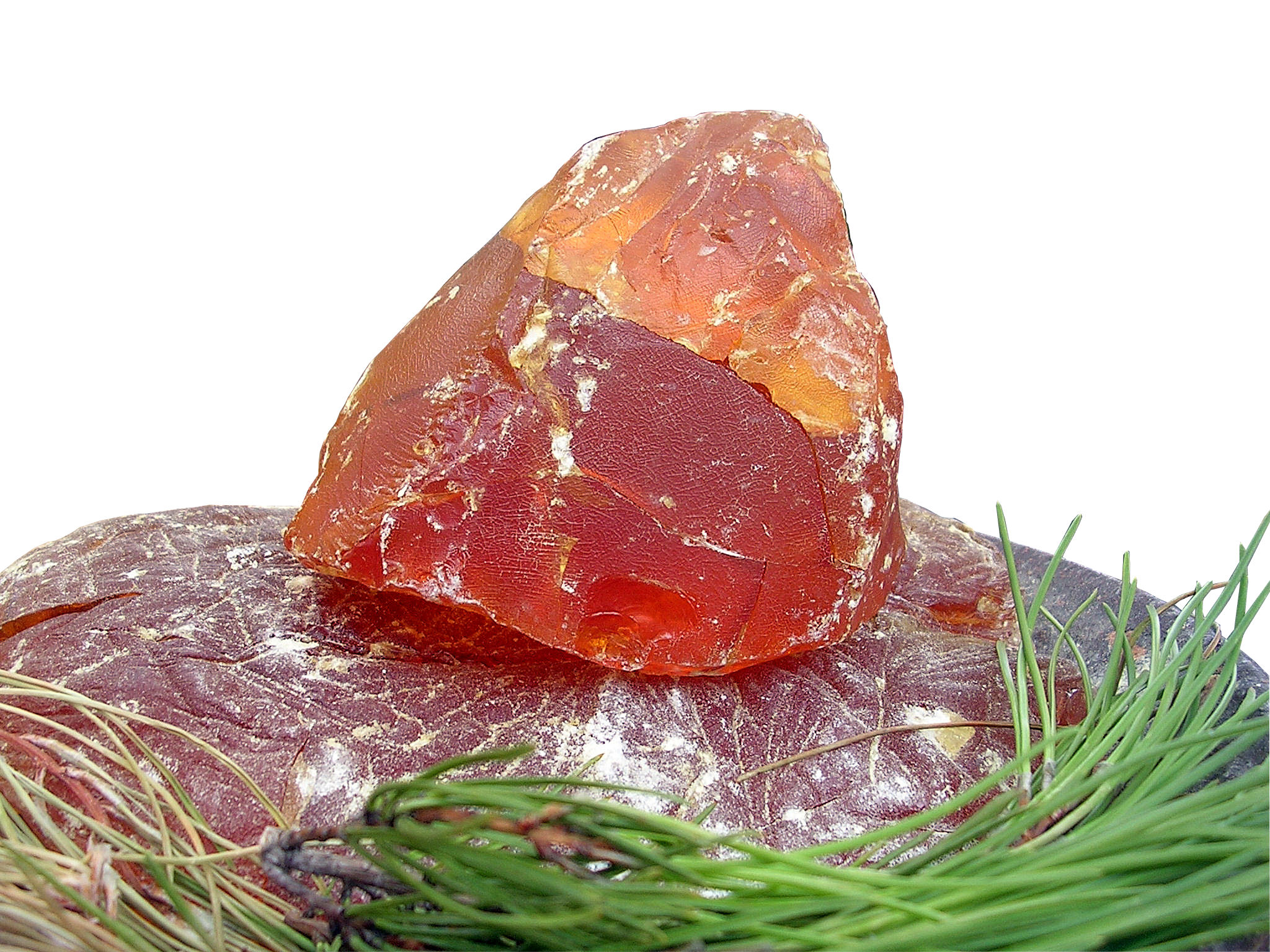
In the early 90s, the mainstream practice in the industry was to remove the flux residues after fabrication, usually through the use of Chlorofluorocarbons (CFCs) and methyl chloroform (now known mainly as 1,1,1-trichloroethane). These compounds are incredibly effective solvents and are cheap to manufacturer — one of the many reasons they were used in countless applications, from hairspray to refrigerant systems to foaming agents¹. As I’m sure all but the youngest readers are aware, CFCs were found to have devastating effects on the atmospheric ozone layer. These solvents have now been replaced by water-based detergents containing surfactants (not unlike dish-soap) and saponifying agents, a change that required reformulating most fluxes to make them more easily washable.
Soldering and Flux
Soldering is the joining of metal surfaces with each other using a low-melting alloy as the proverbial “glue”, without melting the base metals. For the joint to be successful, all surfaces involved must be clear of metallic oxides and other surface contamination.
___________________________________________
¹Foaming agents, or blowing agents, are used to create foams such as polyurethane and vinyl foams. Air is the foaming agent for Italian meringue.
Ensuring surface preparation is the job of the flux. The ideal soldering flux does all of the following when heated.
- Protects the surface from further oxidation, especially necessary as the surface is going to be heated during the soldering process and would oxidize quickly.
- Reduces surface tension. Have you ever tried the experiment where you float a paperclip on water due to surface tension, then add a drop of soap and the paperclip sinks instantly? Similarly, a flux can break the surface tension between the solder and the metal surface, improving the wetting.
- Help spread the heat evenly.
- Reacts with or removes the metal oxides.
- Dissolves the oxides if they’re transformed into metal salts.
When cooled to ambient temperature, soldering flux should:
- Be electrically isolating.
- Leave only transparent and non-reflective residues (to enable optical inspections).
- Leave only thin residues, easily pierced by in-circuit test probes.
- Be chemically inert.
- Non-hygroscopic, to avoid dendritic growth — a phenomenon where a voltage present between two conductors induce migration of metal ions, usually through a hygroscopic medium that has absorbed moisture.
- Be easily soluble in commonly available, cheap, and safe solvents (ideally water).
It’s not (always) possible to tick all the boxes at the same time, but modern fluxes can get close.
What’s in a Flux (Theory)
The different actions required of a flux imply different ingredients in its composition: solvent, activator, vehicle, and other additives.
Solvent
A solvent is needed to dissolve activators, the vehicle, and other additives, while evaporating during the preheating process, or if you forget the jar open… Common solvents are alcohols, glycols, glycol esters and ethers, and water.
Activator
The activator is the main component responsible for metal-oxide removal, and the prevention of its formation during the soldering process.
Activators are what define the “reactive” characteristics of the flux. This includes how corrosive it is and how effective it is at removing oxide.
Common activators inlcude:
- Amine hydrochlorides
- Dicarboxylic acids, for example, adipic or succinct acids
- Organic acids (fruit salad, basically) like citric (yes, the one from lemons), malic acid (commonly present in apples) or abietic acid (from pine tree rosin)
- Halides (not to be confused with halogens; more about this at the end of the article)
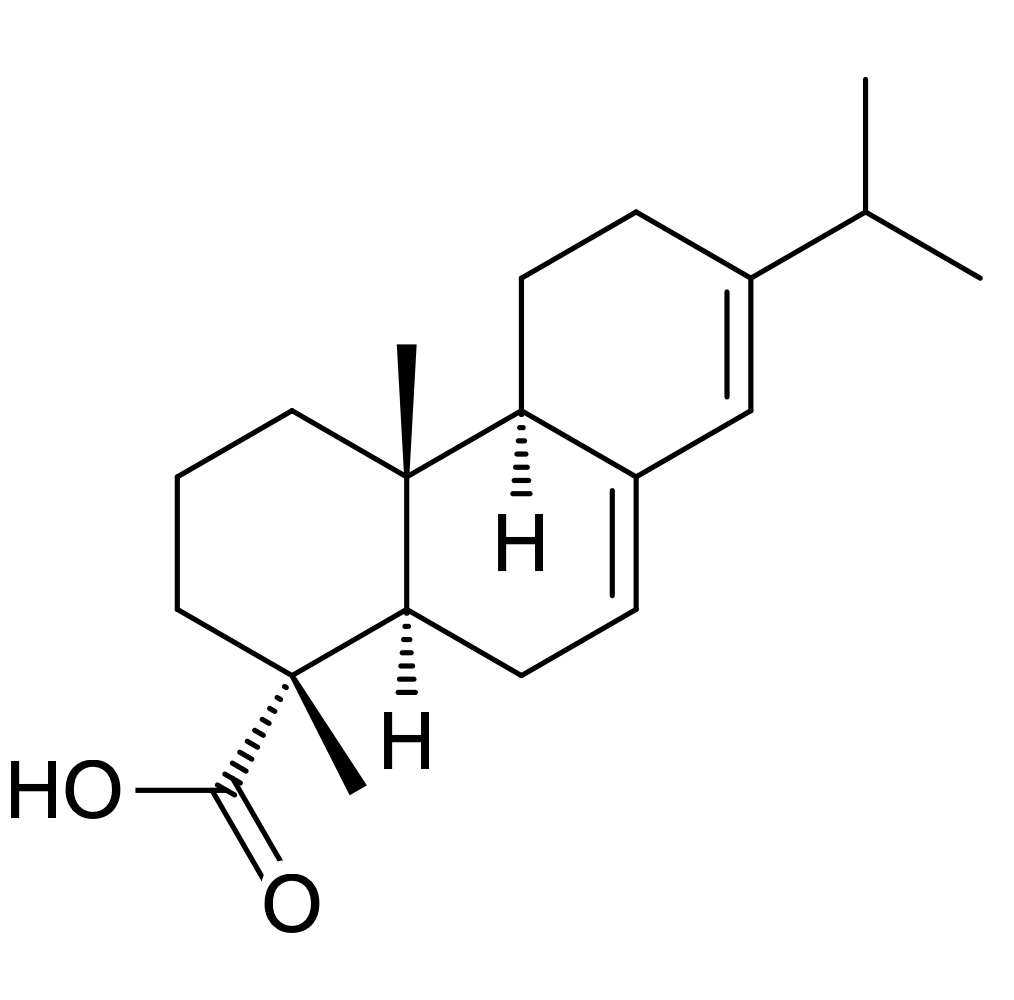
Halides among all modern activators have the best wetting performance and the highest production yields, but are also more corrosive, remaining active after the soldering process. Usually, no-clean fluxes containing halides also contain rosin or other synthetic resins to “stick” the residues in place and avoid corrosion and electrochemical migration.
“Active”, can, for all intent and purposes, be considered a synonym of “corrosive” when discussing fluxes.
Vehicle
The vehicle is a non-volatile liquid or a solid used to coat the surface during soldering and dissolve metal salts (created during the reduction and oxidation reaction between metal oxides and activators).
Example of vehicles are:
- Rosin
- Synthetic resins
- Glycols and polyglycols
- Polyethers
- Glycerine
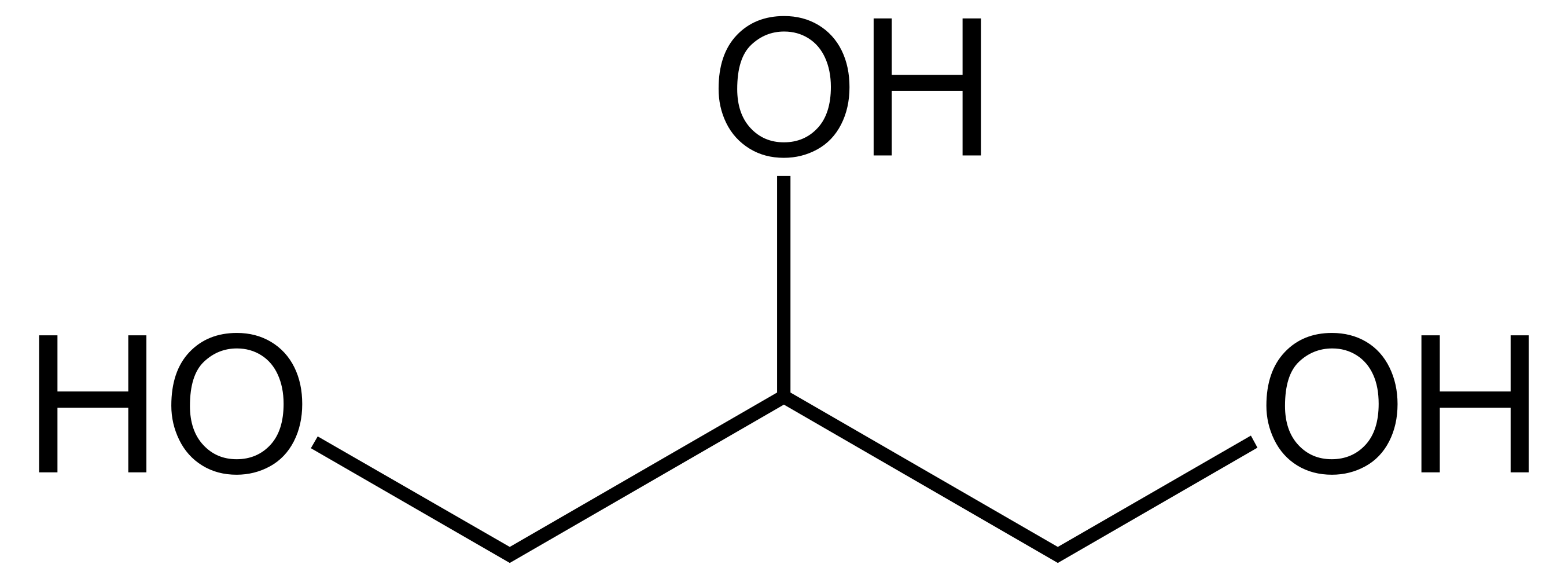
Rosin and resins are the most stable vehicles and have the least impact on reliability, while the others are used primarily in water-soluble fluxes.
Other Additives
Fluxes can contain a little bit of everything, including:
- Surfactants to reduce surface tension and improve the wetting ability
- Foaming agents for foaming-fluxes
- Additives to improve flow or viscosity
- Additives to improve the tack of soldering pastes
- Plasticizers to harden the resins
Types of Fluxes
Fluxes are usually distinguished in a marketing-friendly mixture of composition (for example, rosin and halide-free) and application (for example, no-clean or water-soluble).
The names may sound straightforward and intuitive, but they are meant to make sense from the perspective of a PCB manufacturer and can be misleading to electronic engineers.
Rosin-Based Fluxes and Modern Resin Alternatives
Most fluxes of the past (and still many modern ones) use rosin as both a vehicle and a light activator. There are, however, acids naturally present in rosin,such as abietic acid and dimeric acid. Rosin has long been adopted for this application for a variety of reasons. Most commonly, becuase it can dissolve the metal salts, solidifying and trapping the residues at ambient temperature. In addition, it is easily dissolved into many solvents, it liquifies at the temperatures required by the soldering process, and it’s cheap and widely available.
How active a rosin-based flux is will depend mainly on the activators and the surfactants used. Some activators leave essentially non-corrosive residues, while others, such as halides, can be corrosive if too much of it is left behind. Pure rosin, without any activator, is active enough to solder only a well-cleaned and almost non-oxidized copper surface.
Rosin-based flux is typically divided into four types:
- Pure Rosin (R)
- Rosin, Mildly Activated (RMA)
- Rosin, Activated (RA)
- Rosin, Super-Activated (RSA)
Only R or RMA fluxes have been historically approved for use in high-reliability applications, such as telecom and military.
This distinction has been obsolete for decades. In the 80s, IPC developed the IPC-SF-818 standard, later superseded by J-STD-004A and similarly adopted as ISO-9454, that instead characterizes flux activity by a letter (L, M, H for low, medium, high), a zero for halide-free or a one for flux containing halides, as seen below:
- L0 - Low (0% halides)
- L1 - Low (max 0.5% halides)
- M0 - Moderate (0% halides)
- M1 - Moderate (0.5-2% halides)
- H0 - High (0% halides)
- H1 - High (2% or more halides content)
Additionally, the standard codes for the flux’s vehicle:
- RO - Rosin
- RE - Resin
- OR - Organic
- IN - Inorganic
The two can be combined. For example, REM0 is moderately active halide-free resin-based flux.
Although nowadays rosin fluxes are rarely used in the mainstream electronics industry for board assembly, they’re still widely recommended for board repairs and reworks, thanks to their stability.
It has to be noted, however, that people can develop a sensitivity to rosin if the exposure exceeds recommended amounts. This is the main reason for needing solder fume evacuation equipment when hand-soldering.
While rosin fluxes are generally inert, their residues can interfere with bed-of-nails testing and conformal coating, as well as attract surface contaminants and humidity.
Water-Soluble Fluxes
Water-soluble fluxes are sometimes called “organic-acid fluxes”, a name that holds no real distinction or meaning as almost all fluxes contain organic acids.
When compared to rosin-based fluxes, water-based fluxes are much more active (as always, can be a good thing, can be a bad thing, up to you to decide), work effectively at a broader range of times and temperatures, and have a higher yield due to their excellent wetting action which leads to an improved mechanical resistance of joins.
The downside of all these wonderful properties? Water-soluble fluxes are corrosive and must be adequately cleaned otherwise they will severely impair long-term reliability.
Water-soluble fluxes can contain polyglycols, a substance that can increase the hygroscopicity of the PCB’s dielectric layer. If your boards are subject to extreme temperature variations that can lead to localized condensation, you should beware of this. Together with high voltage gradients, high humidity is the major risk factor for CAF (conductive anodic filaments).
CAF is a failure mode similar to dendrites, but with several differences.
- Dendrites have a fractal appearance, CAFs look like “smudges”.
- Dendrite growth is usually on the surface, CAF is internal.
- CAF appears to be a copper-only phenomenon, while dendrites can be made of copper, lead or tin.
- Dendrites grow cathode to anode, CAF anode to cathode.
- Dendrites are made of metal, CAF of copper salts.
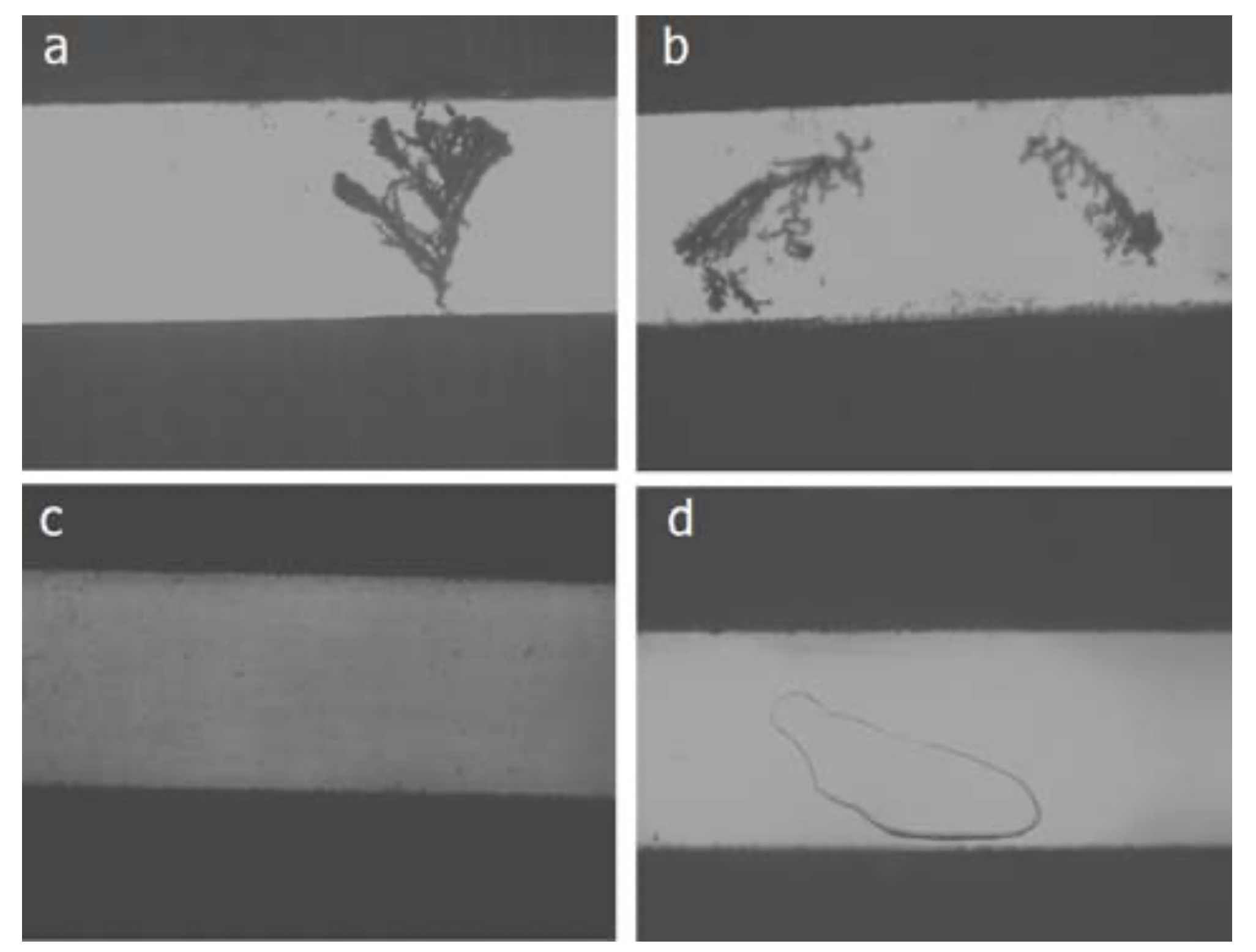
It should be noted that the solvent used in water-soluble fluxes is very rarely water. In this context, water-soluble means that it can be washed off with water, not that it should be dissolved into it before applying.
A critical risk of using water-soluble fluxes is that they often require high-pressure sprays. Many components, in particular switches, cannot survive this washing step without damage. Additionally, water can hardly penetrate under BGAs and is slowed down by densely populated boards, similarly to how eddy water currents naturally form behind the stones in a stream or around skyscrapers.
Advantages of water-soluble fluxes are that they enable the best adhesion of the conformal coating and have the least impact on the dielectric properties of the substrate, thus they’re ideal for RF circuitry.
No-Clean Fluxes (Low-Solids Flux)
Up until the mid-1980s, most fluxes had a high solid and non-volatile fluid content, typically 25 to 35 percent by weight. Early modern fluxes composed mainly of weak organic acids had a 5 to 8 percent content of solids. Nowadays, many modern “no-clean” fluxes have just one or two percent.
The name of these fluxes changed from “low-residue” or “low-solids” to “no-clean”, a name that is only proper if the residues are non-corrosive.
From the 90s onward, fluxes started to appear on the market with water-based solutions to cut on the use of VOC (Volatile Organic Compounds).
Today over 70 percent of electronics worldwide are manufactured with no-clean fluxes. While they are much harder to use (as the temperature ranges can be very restrictive), with careful implementation they enable the manufacturer to skip the cleaning process and save money.
The advantages of no-clean fluxes are mainly related to the lower costs and reduced environmental impact. They have, however, a series of disadvantages.
- Bed of nails: no-clean residues can be hard and slip through masking and reach the bed of nails test point, impairing testing.
- Difficulty of inspection: the brittle, transparent residues often look like a cracked solder joint, making inspection difficult.
- Can inhibit the adhesion of the conformal coating, as the residues are left on the board.
- Corrosive if left unheated.
The latter disadvantage is something that very few engineers are aware of, but it’s of the utmost importance! No-clean fluxes are corrosive out-of-the-box and become non-corrosive only after proper activation.
If you rework or repair a board using no-clean fluxes, a great degree of care must be taken when using them. For example:
- Use only flux-core soldering wire and no other flux, ensuring all the flux is activated by heating it
- Minimize the solder wire diameter
- Minimize flux usage
- Do not use dropper-applicators
- Never mix different no-clean fluxes unless expressly allowed by the manufacturer
- Do not clean no-clean flux as cleaning will just spread the residues further — instead, de-activate it by heating
- Bake the boards to activate any residual flux
Appendix
Halogens and Halides — What’s the Difference?
In the electronics industry, we often confuse the term “halogen” with “halide”.
A halogen is an element in the 7th column of the periodic table, such as fluorine, chlorine, bromine, iodine and astatine. Astatine is one of the rarest naturally-occurring elements, and iodine is not really used in our industry, leaving us with the former three.
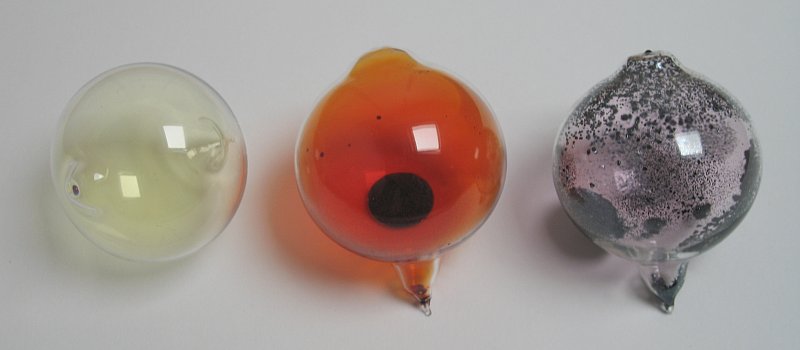
The halogen Bromide has often been added to polymers (plastics) — including many used as electrical insulators — as a flame retardant. Halogens are being phased out for a couple of health reasons:
- They form dioxin (a known carcinogen) when burned.
- Electronics with bromide can emanate corrosive fumes when burning; in server farms, one single fire can increase the risk of subsequent failures due to contamination from these fumes.
Halogens were first introduced to replace PCBs, and have been banned almost worldwide since 1979. Wait, what? This time, PCB means PolyChlorinated Bis-Phenols, not Printed Circuit Boards.
Halogens have seven valence electrons (electrons available for chemical reactions) and are thus extremely active. They are potent oxidizing compounds as they want to get an eighth electron. When they achieve this goal, they become a halide. Examples you might have heard of are Sodium Chloride (table salt), Silver Chloride (photographic film), Hydrogen Chloride (the acid), and Calcium Chloride (street de-icing salt). Once they have this eighth electron, they don’t want it anymore and become reducing agents.
In general, halides are used as flux activators and Halogens as flame retardants for the PCB substrate. In rare exceptions, Halogens might be used as an additive in fluxes to enhance high-temperature performance.
A halogen-free flux is also halide free, although the opposite is not necessarily true.
Conclusion
Now you know everything you never wanted to know about fluxes, and you’re probably even more confused than before. What now?
In a previous article [INSERT LINK], I published a free Draftsman template that included numerous board specifications you might want to communicate to your EMS house. Draftsman is part of Altium Designer and enables you to create and update board documentation in minutes instead of days. To be candid, it’s my favourite part of Altium Designer… I’m a bit of a documentation-nerd, and Draftsman generates some of the most beautiful documents in the industry.
If you’re not sure if you want to conformal-coat your boards or not, but you still need to manufacture the first batch, you should choose a water-soluble flux, as it will allow the grated degree of compatibility with conformal coatings.
Emails and phone calls will get lost, but a Draftsman document acts as a single source of truth for PCB Manufacturers.
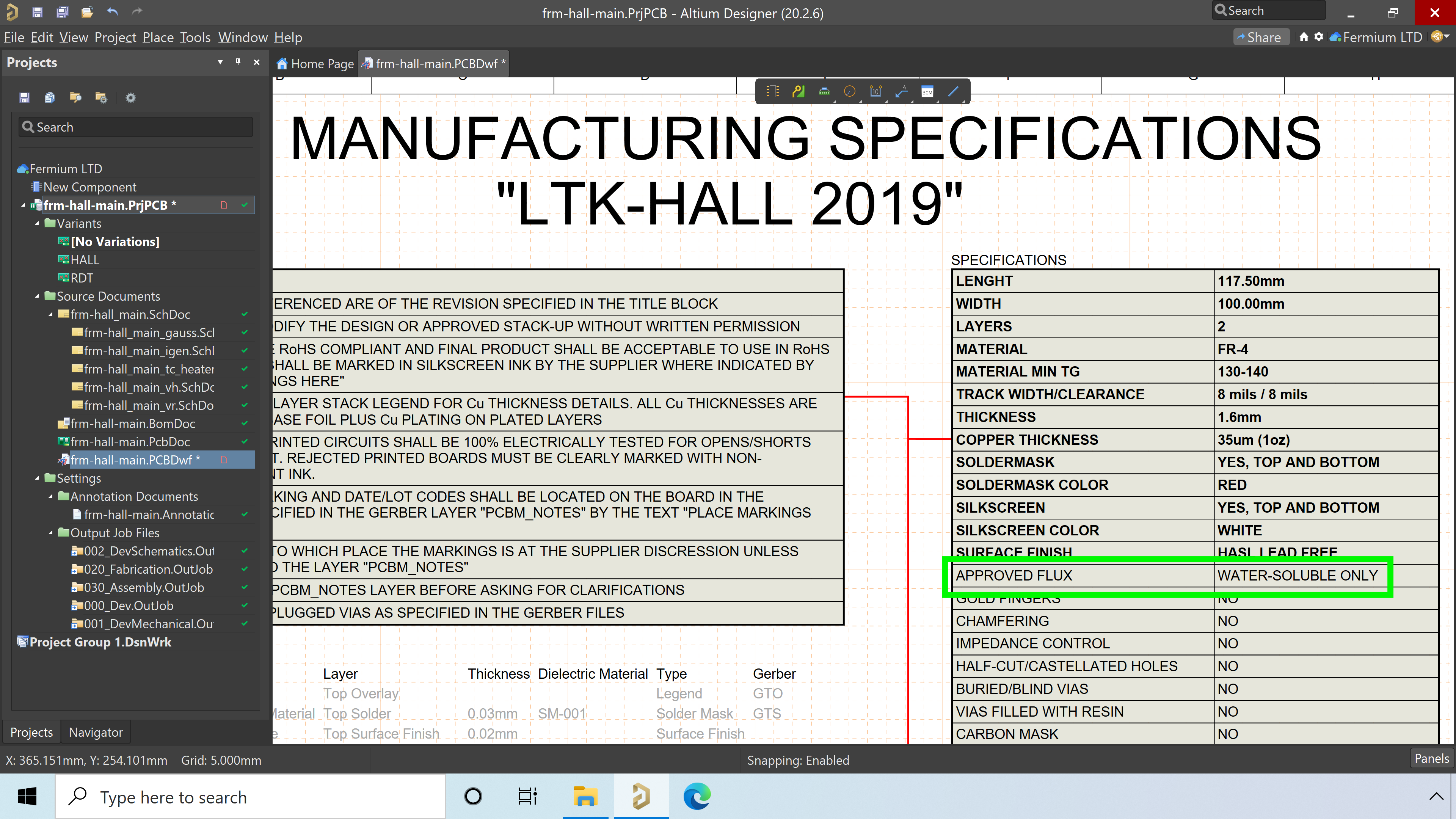
If you have an active A365 subscription, you can release your document through the cloud and share it with your manufacturer in one click; no need to zip or manually curate manufacturing packages.
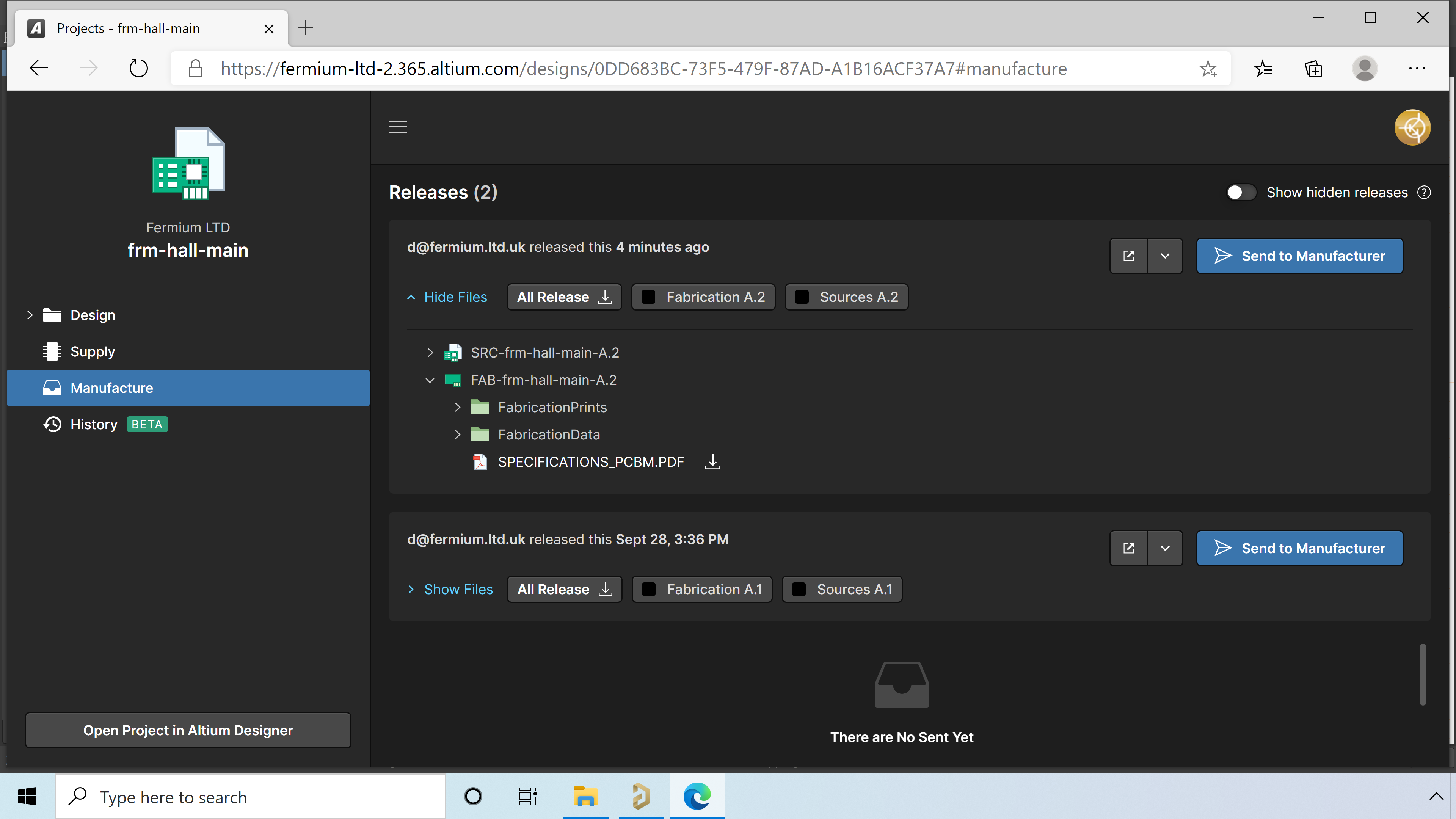
Your manufacturer will even be able to take advantage of Altium 365 online viewer to view PCB, Schematic, 3D PCB and BOM, with full cross-linking between components and nets in the different modes.
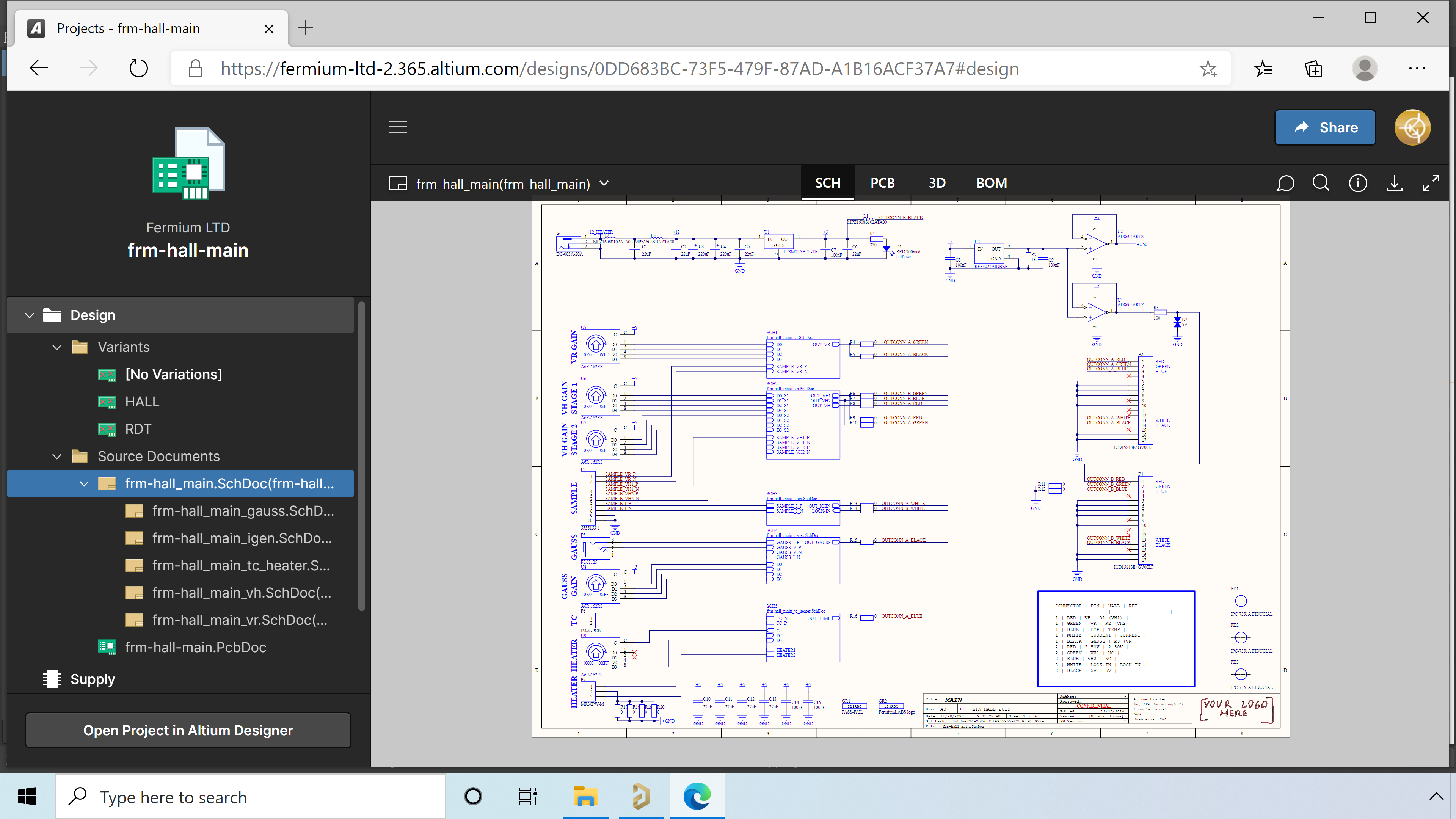
The design tools in Altium Designer® contain everything you need to keep up with new technology. Talk to us today and find out how we can enhance your next PCB Design.