State of the Electronics Industry 2021
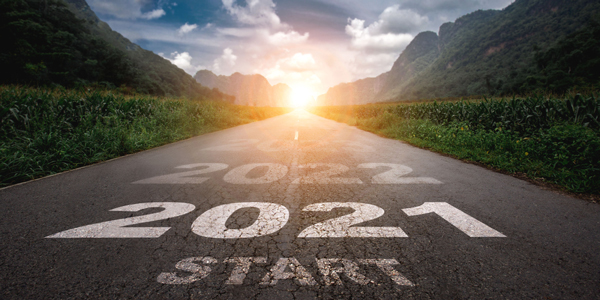
With the challenges of 2020 behind us, what challenges and opportunities lie ahead for hardware designers in 2021? In this article Vince Mazur, Technical Product Marketing Engineer at Altium, looks ahead to three emerging trends and share steps to address each one successfully in the year ahead.
Introduction
It's an understatement to say that 2020 is a year that we won't soon forget. Last year imposed many new challenges on all of us-- specifically electronic product designers. Currently, things are looking up with the arrival of vaccines and lowering hospitalization rates. However, 2021 will likely continue to be influenced by many of the same dynamics as 2020. Additionally, the fast-moving electronics business will continue to bring about pervasive design challenges in 2021 that have little to do with factors outside of our industry.
In this article, I will address three challenges from the electronics design perspective. These include continued work from home, electronic component shortages, and virtual education. In each section, I will list some things you can do today to cope with these challenges, and I will close the article with a summary.
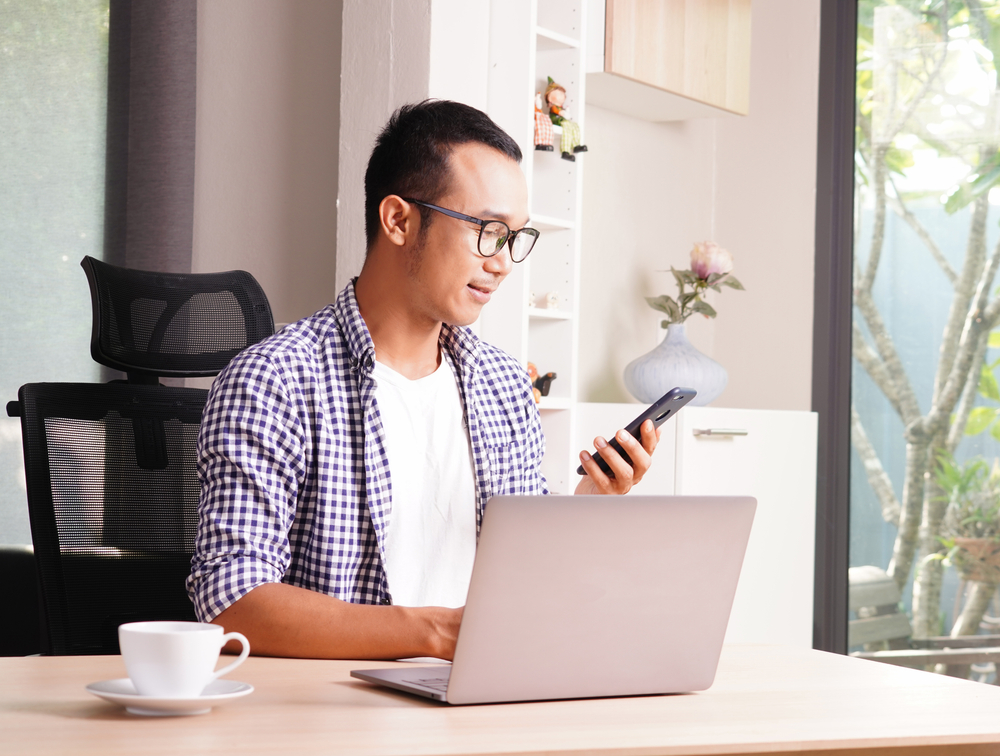
Continued Work From Home
Electronics design is a team sport. Even solo product developers need to collaborate with various individuals and companies that include manufacturer representatives, FAE's, board fabricators, contract manufacturers, potentially outside contractors, and more. Simultaneously, the complex mix of electronics design on a good day, under normal global circumstances, is loaded with headaches, challenges, and risks. It's just the nature of the exciting field of electronics design. While there are some benefits to working from home, the inability to collaborate in person continues to be problematic.
For medium-to-large organizations, the situation is even more complex. The physical topology of these organizations ranges from a single site to a globally connected network of sites. While there are exceptions, the primary collaboration method had been face-to-face communications, with videoconferencing between remote or global locations used as required. Discontinuity results naturally from disparate teams responsible for specific key product domains within a product or system design. The need for design team collaboration and strong communication between domains, such as ECAD and MCAD, is critical for success. These things were challenging before the pandemic and have been made more difficult by physical separation. Furthermore, the lack of access to vital well-equipped company labs that may contain millions of dollars of test and measurement equipment continues to create serious issues.
While some professions (sales comes to mind) were early adopters of working from home, electronics product engineering has not been widely accepted due to this need for lab access and collaboration. The transition many electronics OEMs made from their centralized locations and workforce to fragmented teams working individually from their homes created increased challenges. Designers, accustomed to interacting as a team, found themselves isolated to home offices. Fortunately, a fast pivot to use cloud-based tools, such a Zoom, Dropbox, Google Drive, and others, enabled teams to remain connected. Here at Altium, we had just released our new cloud platform, Altium 365, which was the first platform of its kind that allowed an effortless extension of the complete electronic product design environment to users anywhere there was an internet connection. The result was that the cockpit view if you will, was identical at home to how it was at the office.
Even as designers begin to move back into their offices, the working environment will likely be considerably different from the pre-pandemic atmosphere, especially in the area of face-to-face communications. Distancing will likely continue to be a watchword, and collaboration will likely suffer some inefficiencies due to the continued precautions.
Steps You Can Take Today
Here are some suggestions for steps you take today to optimize your work at home experience:
- If you haven't already, establish a standard "stack" of tools tuned to the unique needs of electronics design and collaboration, including virtual meetings, comment and markup tools such as Slack, design creation, PCB design, centralized part library access, and a shared design data repository. The key here is to ensure that everyone on your team is using the same foundation. Once back in the office, all work and related data created from home can be migrated back into the corporate foundation already in place without compromise or inconsistency.
- If the lack of lab access is problematic, consider relocating company equipment to your home or lease test equipment for your at-home environment. Also, consider increasing the amount of simulation you perform. In-schematic simulation capability is available today and contains many analysis features that are essentially virtual test and measurement instruments that may be of great assistance.
- If you are involved with embedded software development, consider augmenting your code development with the code simulation capability. This simulation is available in many leading IDE's, such as Microchip's MPLABⓇ X. If your embedded software team typically requires hardware targets, consider abstracting out the architecture into behavioral code that can mimic the target hardware. Perhaps this will not be a perfect replacement for target hardware. Still, it will undoubtedly help progress needed software development so that when hardware/software integration is performed in the lab, the software will be far closer to specification.
- Don't marginalize the need for social interaction. We're social by nature, and we've all had ups and downs during this time. There has been some useful material written on this topic, such as the following article that you may want to consider reviewing: https://www.mayoclinic.org/diseases-conditions/coronavirus/in-depth/teleworking-during-coronavirus/art-20487369.
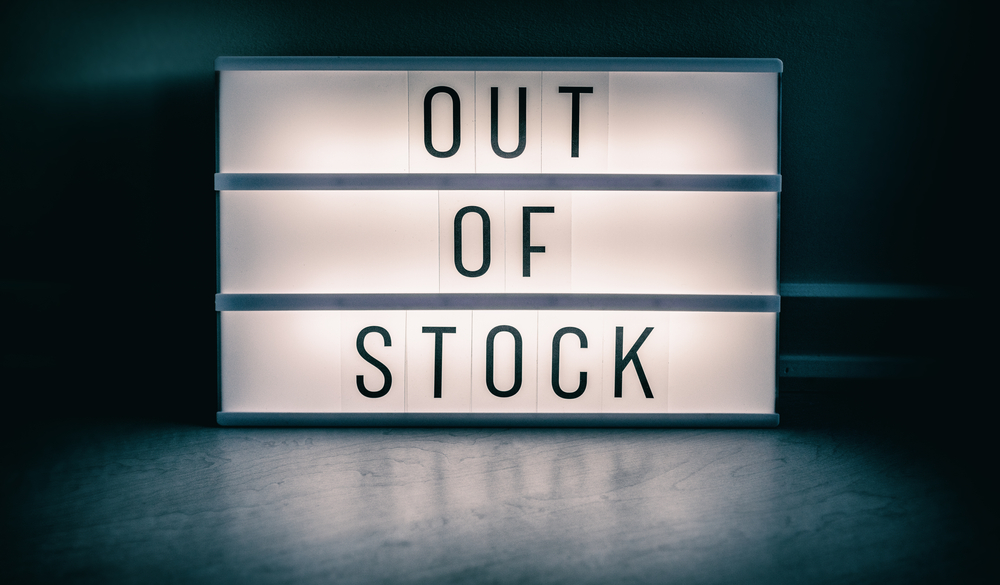
Component Shortages
The global pandemic, combined with the impact of a backlog of orders, has created significant component shortages in 2021. Reports show that several automotive manufacturers have had to close down assembly lines because key electronic components required for production are not available. Small companies are left to compete with larger companies for available parts stock. Unless there are contingencies already in place, there will be a growing trend of companies facing detrimental manufacturing delays due to the current shortages. In turn, this situation could compel companies towards risky sourcing decisions for components that turn out to be counterfeit. Counterfeit parts alone are estimated to cost manufacturers $7.5 billion annually in lost revenue. Against this backdrop, consider that IHS MarkitⓇ, the world's most accurate component intelligence source, says that an average of 15 end-of-life (EOL) notices for electronic parts are issued every day. It is worth noting here that IHS Markit is available as part of the Altium Pro Subscription Plan.
Managing BOM costs and selecting components or their alternatives is more complex than ever as obsolescence, stock-levels, counterfeits and environmental non-compliance challenges continue to build. It is critical to ensure that the components you need for a manufacturing run are available before the job is submitted. The alternative is a frustrating cascade of events that can lead to unnecessary production delays. While it is difficult for organizations to insulate themselves from all component-related risks, many can be avoided with proper contingency planning.
Steps You Can Take Today
- Proactively make provisions for contingency from the beginning. Before saving a component in the library, ensure that there are at least three manufacturer part numbers that meet the specification for that component. Rank each part number based on important factors to your project, such as cost, tolerance, and working voltage.
- The key is to have qualified, simulated, or even lab-tested alternatives established before using the new library components. If you have an existing library, specify alternative part choices for each component. Many aggregators, such as Octopart, can enable you to rapidly find similar parts along with giving you insight into current stock levels.
- For existing designs in production and work in process (WIP), review and "scrub" the BOM more frequently for early identification of any issues or trends. While tools such as Altium's ActiveBOM will do this automatically, the time required to perform this manually with a spreadsheet will more than make a favorable return as valuable insurance.
- Design for maximum substitution and therefore availability. It is counter-intuitive to realize some circuitry with discrete components when a nice IC is available to do the same function. But, when the IC has unreliable stock, using a discrete design may offer more flexibility in assuring you can go to production. Frequently, discrete solutions are lower cost than IC options, but this varies on a case-by-case basis.
- Establish safety stock for essential line items. There are times when a design must use a device that is required to achieve specifications and cost targets. For those situations, buy excess reels and keep them on hand for insurance stock. It's not uncommon to see manufacturing delayed by a 4 cent component. Implementing this practice just might become the lowest cost insurance you may ever have.
- Make accurate and timely data-driven decisions by using comprehensive and real-time component data whenever you can. Sites such as Octopart offer no-cost access to component data that is very useful for these purposes. Commercial platforms such as Altium 365 close the gap even further and, when augmented with IHS Markit® electronic component supply chain intelligence, extends Fortune 100 level information into the hands of smaller organizations and even individual designers.
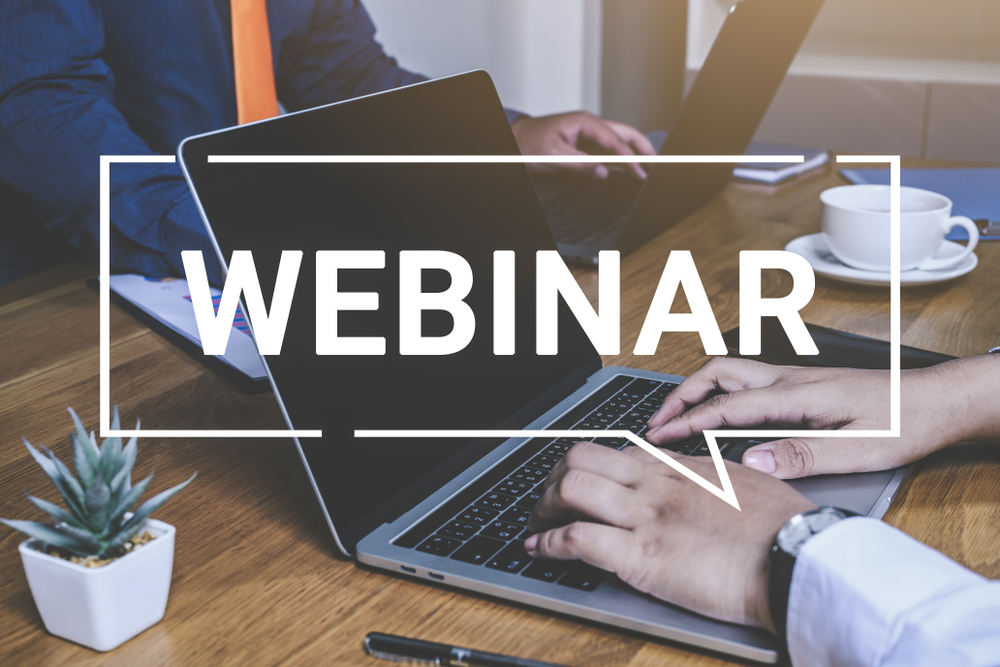
Virtual Education and Events
A continuing commitment to education has long been part of the electronics industry landscape. Electronics have always advanced at a far greater pace than most other fields, and the rate of change continues to accelerate over time. Staying current on the state of technology and its related challenges is an implicit requirement of the career. You will be left behind if you don't stay current and implement the latest best practices.
Events such as classes, workshops, conferences, and trade shows have been a common way to stay abreast of new developments, challenges, and solutions. These traditional sources of education and information exchange have been eliminated or postponed in this post-covid era. In their place, a plethora of virtual events, webinars, and online training has arisen. While Designers have always spent many hours in front of a screen, the replacement of tradeshows and daily in-person meetings by virtual interactions tipped the balance of screen time to a point not seen before and are causing screen-fatigue and digital burnout.
In-person education and event participation offers many advantages over their virtual counterparts. Live events and education often deliver a welcome change of scenery and much-needed time away from computer screens. Off-site events give design engineers valuable opportunities to focus on professional development. Additionally, engineering team leaders can onboard knowledge and resources that they can take back to their teams. External event venues offer priceless opportunities for enriching group discussions and networking.
Practically speaking, comparable benefits are available in virtual settings. While rich resources are accessible through cloud and online events, this does little to address screen fatigue, home distractions, and the stressors resulting from isolation and remaining at your desk day after day.
Steps You Can Take Today
- Create or personalize your learning venue or space. Rather than being bound to the same home office desk for virtual events, consider using another room or location. The change of location may mitigate some of the sense of isolation and meet your need for a change of scenery. If space is not available, shut down your email and work apps and only have the tools open you need to participate in the event. If appropriate, silence or turn off your phone. Use your smart TV or Google Chromecast to allow you to view your virtual education or event on television. Whatever works for you, but the key is to minimize distraction and maximize focus. Sometimes great things happen when we change venues.
- Set your objectives and expectations before attending. Outline what you want to get out of the event. Do you have specific questions you would like answered? Do you have a collection of resources you would like to receive? Are there specific networking opportunities you are pursuing? Establishing a list of takeaways that define successful participation can be a great way to ensure the event delivers for you.
- Take great notes. Whether it's a conventional notepad or an editor open on your system, make a determined effort to take good notes. Is something being discussed that is relevant to a current project? Could you write it down? Does something you've just heard initiate a creative spark? Then, write it down and employ the basic fundamentals in place that you'd typically use at an off-site event.
- If possible, attend events that can be scheduled outside of regular working hours or are available on-demand. This way, you can schedule participation at a time that aligns with your lifestyle and preferences. However, be mindful that many live events offer interaction and Q&A with experts, aspects that you will forfeit for the convenience of on-demand learning.
- Seize the opportunity to engage. Participate in virtual meeting rooms, chats, Q&A sessions. Putting forth a conscious effort to verbally and visually interact with industry peers and fellow attendees can offer beneficial information and fill some of the gaps left by the physical isolation some may be experiencing. Participation also has the secondary benefit of keeping those professional socialization skills sharp and polished for the eventual return to normalcy!
Summary
In this article, I reviewed some of the current challenges facing electronics designers in 2021, with the pandemic hopefully winding down. These challenges included the continuation of working from home, current electronic components shortages, and maximizing the value from virtual education and events. I've put forward some steps that may help meet each of these challenges. I hope you found this information helpful and beneficial in helping you further your professional efforts.
While 2020 provided many stressful challenges, the companies, and individuals that continue to overcome them have risen to meet these challenges by becoming more adaptable and resilient. As we venture ahead into 2021, I believe the hard-won lessons of 2020 and the spirit of adaptability and resilience will continue to provide value to your engineering career and the company you serve.