Design Your Metal Core PCB in Altium Designer
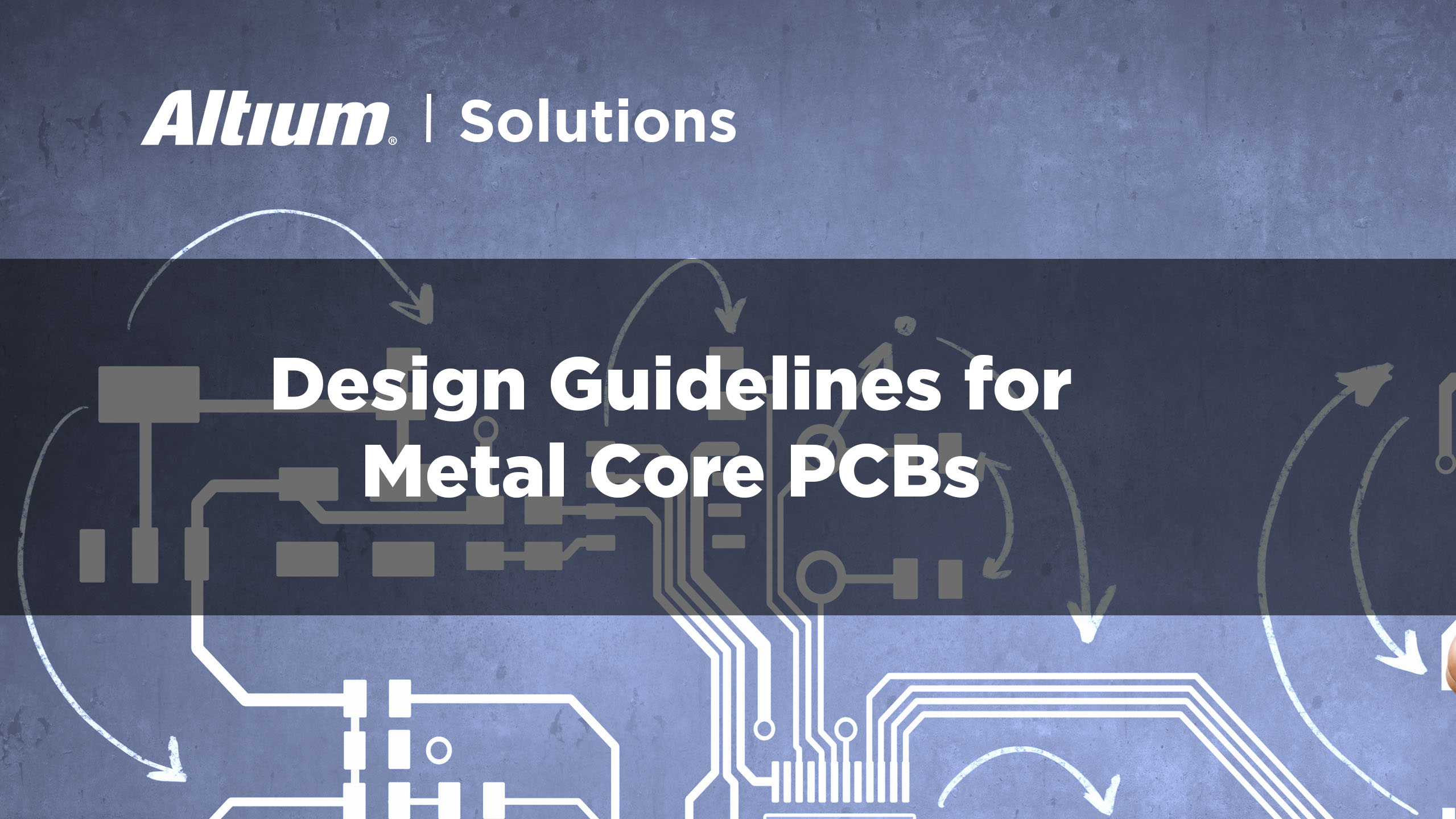
Most printed circuit boards use a thick FR4 core layer to provide structural stability and interior copper layers for a multilayer PCB. If problems like excessive heat and low thermal dissipation are required in your particular application, you might consider designing with a metal core PCB. You’ll see other advantages like greater structural integrity, as well as a natural EMI shield thanks to the internal metal core.
These circuit boards require some specific design guidelines to ensure they can pass through the standard metal core PCB manufacturing process. With Altium Designer, you can satisfy the major design requirements on metal core PCBs for any application, and you’ll have the tools you need for accurate placement, and multilayer routing on your metal core PCB. If you’ve never designed a metal core board, keep reading to see some important design guidelines you can implement in Altium Designer.
ALTIUM DESIGNER®
A unified PCB design package with multilayer PCB design and layout tools for specialty circuit boards like metal core PCB layouts.
Most PCBs used in consumer electronics, and even in more demanding applications like automotive and aerospace, use standard PCBs built entirely on glass-filled around epoxy resin laminates. Printed circuits on FR4 core materials are plated with copper foil on each side, and multilayer stackups are built by etching copper on each layer, followed by placing a low thermal conductivity resin layer as a prepreg between the next layer in the stack. This stack is then bonded using heat and pressure. After successive steps, you have a multilayer PCB.
These standard resins come with a narrow range of possible material properties that are determined by the resin content and type of resin impregnated in the PCB laminate. There are some drawbacks seen in standard FR4 laminates that are not ideal for certain applications:
- Low thermal conductivity compared to materials like copper or aluminum
- Losses in most FR4-grade laminates are too high for some RF applications
- These materials can have experience high expansion at high temperature
Metal core PCBs are one possible alternative to printed circuit boards built on FR4 laminates. Using a metal core in the central layer of the board, or as a backing layer on the board, gives the design very high thermal conductivity, as well as a simple way to create a grounded EMI shield for the design.
If you follow the right design guidelines and use the best PCB layout software, you can create a metal core PCB that can be fabricated at scale. Follow these guidelines to make sure your metal core PCB is manufacturable and follows basic industry standards.
Important Design Guidelines for Metal Core PCBs
There are many important design guidelines in a metal core PCB that should be considered when creating a stackup with a metal layer. Metal-core boards are normally built with the metal layer used as a core layer in a low-layer count stackup. Aluminum is normally used as the metal layer in the stackup, although copper or stainless steel could also be used.
After determining the metal material and selecting standard dielectric laminates, the layer arrangement needs to be determined. The layer stack will then determine some important aspects of routing and component selection:
- Metal-backed PCB: The metal layer is placed on the back side of the board, and components are present on the opposite layer. Traces cannot be routed on the back layer, although through-holes can be used to route between dielectric layers and bring ground to the metal layer.
- Metal core PCB: This version can be a double-sided board, and routing can pass between each side of the metal core using plated through-holes. Multilayer dielectric stacks can be used on each side of the metal core, which will support routing on multiple layers.
The metal layer should be grounded so that it can provide shielding and so that it will not act like a big monopole antenna. Specific applications may require mourning the metal core to an enclosure, an important point to consider when designing for aerospace and defense PCBs.
Metal Core PCB Applications for Military and Aerospace
Military and aerospace are two areas where printed circuit boards must be able to withstand repeated thermal cycling, extremes of temperature and moisture, and frequent mechanical shocks. Metal core PCBs help satisfy these operational requirements as they provide greater structural integrity and thermal conductivity than boards built on FR4 laminates. The higher thermal conductivity of these boards helps ensure the temperature distribution in these boards is uniform during thermal cycling, which prevents hot spots from forming near active components.
Other applications include boards for high-current regulators, boards for high power LED lighting systems, automotive electronics, and other products that must operate at elevated temperatures. Designing for any of these applications starts with building the right stackup and choosing a board architecture that can ensure low temperature with high reliability.
- If you’re building a brand new circuit board with a metal core PCB, you’ll eventually need to move your device off a breadboard and build a PCB prototype.
- FR4 PCB laminates and metal core boards are not your only options for PCB substrate materials.
Learn more about selecting alternative substrate materials, such as ceramics.
- Another alternative to FR4 PCB substrates is ceramic materials, which can provide very high thermal conductivity.
See Learn more about the advantages of ceramic materials for PCB substrates.
You can create complex power planes in your metal core PCB with the layout and polygon design tools in Altium Designer.
Metal Core PCB Manufacturing Process
Metal-core PCBs must follow a particular process due to the presence of the metal layer in the stackup. If the board is a single-layer boards with no layer transitions back to the metal plate, then the standard process used with FR4 dielectrics can be used, where the dielectric layer is pressed and bonded to the metal plate.
For multilayer dielectric stackups, the metal core must first be drilled to allow for a layer transition without creating a short circuit. First, slightly larger holes are drilled into the metal layer, and the holes are plugged with an insulating gel. This gel is cured and hardened, which now allows it to be plated with copper, just like a standard via. The rest of the stackup is pressed and bonded with the metal layer, and through-holes are drilled through the stackup, followed by plating and cleaning.
Choosing Circuit Board Components for Metal Core Boards
Whether you are planning to manufacture a PCB on FR4, a rigid-flex PCB, or a high thermal conductivity metal core PCB, you’ll need tools in your design software for sourcing circuit board components. Surface-mount components are preferred in metal-core boards as they have no risk of shorting to the metal core layer. However, through-hole components can be used, although care needs to be taken to ensure the solder does not wick through to the back side of a metal-backed board.
- There are a number of steps involved in fabricating any circuit board. The right design choices can expedite the process and help you avoid unnecessary redesigns.
- Your manufacturer will need a complete documentation package that shows all fabrication aspects and components that appear on your metal core PCB.
Learn more about generating a complete documentation package for your manufacturer.
- Metal cores are just one option for aiding thermal management in your PCB. Other passive techniques are useful for keeping your boards cool and for removing heat.
Learn more about working with thermal pads or thermal paste.
Design all aspects of your metal-core PCB and select the best components in Altium Designer
Metal Core PCB Design in a Unified Environment
Designing a multilayer metal core PCB can be a difficult process if you don’t have access to the right design tools. You’ll need layout tools that allow you to accurately place components, route traces, define vias, crosscheck electrical and thermal loads, and many other aspects that go into designing any PCB.
If you’re designing a metal core PCB, you’ll need a complete library of stackup materials and a circuit board layer stack manager that gives you full control over the structure of your board. With the best PCB stackup manager, you can design a stackup that specifies the location of the metal core, either as a symmetric or an asymmetric stackup. After defining your dielectric layers, you’ve down the important groundwork needed to start placing components and routing traces.
Altium Designer Has All the Best PCB Layout Features
Altium Designer makes it easy to use schematic capture to import components into a blank circuit board, and you’ll have ultra-accurate CAD features for placing components. Routing on each layer is also easy with a complete suite of routing features, and the layout engine will check your board against important metal-core PCB design guidelines as you create your board. No other design platform helps you stay this productive as you work through complex designs.
- Working with any metal core PCB requires access to a complete library of standard materials and the best PCB layout tools you can find.
Learn more about the complete set of PCB design tools in Altium Designer.
- Metal core PCBs often have complex enclosures and specialty mechanical components, and Altium Designer includes the native 3D design tools you need for metal core PCB design.
Learn more about Altium Designer’s native 3D PCB design features.
- Altium Designer lets you quickly release your metal-core PCB design to your collaborators through the Altium 365 platform, the only cloud platform that lets you share and collaborate on complex circuit board designs.
Learn more about sharing your PCB project data with Altium 365.
You can create high-quality metal core PCB layouts in Altium Designer
When you work with Altium Designer, you’ll have access to a full suite of PCB design tools that ease the design process for any circuit board. Other PCB design software companies force you to cobble together multiple programs to complete your designs. Instead of trying to force multiple programs to work together, you’ll have a single platform to produce high-quality PCBs and bring them to high-volume manufacturing.
Altium Designer on Altium 365 delivers an unprecedented amount of integration to the electronics industry until now relegated to the world of software development, allowing designers to work from home and reach unprecedented levels of efficiency.
We have only scratched the surface of what is possible to do with Altium Designer on Altium 365. You can check the product page for a more in-depth feature description or one of the On-Demand Webinars.