Managing 3D Models for ECAD/MCAD Data Transfer
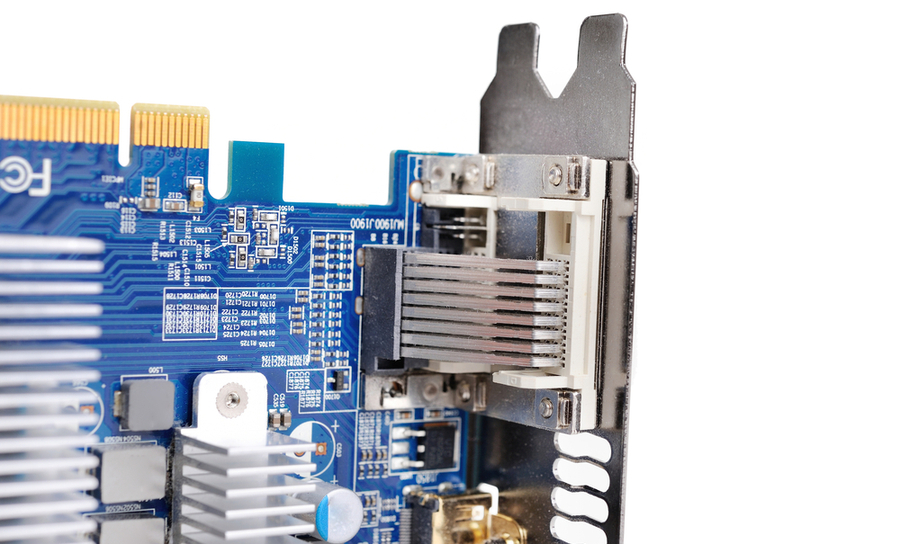
Communication is tricky when oppositional semantics fail to play well together. This sentence is a good case in point. When ill stated, information is rarely understood. The same goes with software infrastructures. Many do not play well together when information in one is defined differently in another.
3D models of components for use by mechanical and electrical CAD programs are historically represented quite differently across platforms. This makes design developments tricky when collaborating on the same device. Transferring a simple component model can lead to hours of refinement during the transfer.
Without automatic and accurate translations, MCAD and ECAD program users struggle during design developments. Accurately representing dimensions and keepouts for mechanical dimensioning can take weeks or months to establish. Handoff to electrical CAD programs can ruin months of intricate dimensioning, leading to error-prone PCBAs during manufacture.
Ensure your design process doesn’t get hung up on board shapes between mechanical engineers and purchasing. Don’t offshoot your collaboration server, trust your step model and PCB layout information. Altium Designer® built their ECAD program to work seamlessly with mechanical .STEP files for easy sharing between MCAD and ECAD programs. This allows trusted management of 3D models throughout design and development.
ECAD/MCAD Struggle to Play Well Together
Historically, ECAD and MCAD software has led designers into manual operations to capture intricate details of 3D modeling. This leads to development slowdowns, costing enterprises’ loss of time and money when bringing products to market. Designers are left to struggle with hint maps defining mating operations across the tools.
Hint maps define the manual process for communicating coordinate origins for 3D models. Coordinate origins for the same models are defined in ways that are not recognized by downstream software tools. When it is time to transfer the files, mating operations are not written and dimensions do not transfer.
3D modeling ensures components fit well together
Attributes defining details of 3D models do not port across ECAD and MCAD. Transfers are incomplete and the information is lost. Time is required by designers to manually review and input intricate dimensioning information into the downstream tool. It is a difficult process with room for error.
Tricky Communication Between Tools Induces Failures
MCAD tools define coordinate systems in ways ill understood by ECAD programs. Ad hoc development of tools required to communicate identical information leads to mistakes. Developers spend valuable time visually reviewing details from one tool to another. Mistakes are made when configuration details are missed.
MCAD assigns attributes to 3D models that are missed when transferring files to ECAD. Missed attributes from idx files also mean that dimensions defined must be researched for proper placement in 3D ECAD models. Files sent for fabrication contain vital details and induce failures in PCBs.
Confidence Builds With Trusted ECAD/MCAD Partners
Lagging confidence is restored when both ECAD and MCAD software use the same file formats for 3D modeling. The configuration of coordinate systems is represented identically across platforms. Importing and exporting from MCAD to ECAD, and back again, is automatic and trusted. Validation is repeatable across the platforms.
File formats for 3D transfer seamlessly across MCAD and ECAD. Attributes port automatically, retaining all information needed to propagate through the ECAD drawings. Naming conventions remain and dimensions are accurately ported, so 3D modeling can be trusted. Partners have no need to manually review visual representations or ported dimensions of the 3D model.
Altium Designer Works Well With MCAD .STEP Models
Altium Designer incorporates collaborative 3D modeling within their EDA tooling. Models may be directly imported from vendors for use within Altium’s Schematic and PCB editors. Alternatively, dimensioning and 3D models created in MCAD programs can be directly imported into Altium’s editors using .STEP files.
Model components in 3D for dimension checks
Altium Designer provides a 3D PCB Editor that allows full utilization of 3D modeling. Shapes can be created within the editor or the editor can import models from mechanical engineering software tooling. Within the PCB Editor, full access to rotating and positioning the 3D models is available with the mouse. Within the unified environment, shapes are easy to view by zooming, panning, rotating, or re-orienting.
For 3D model sharing, Altium Designer’s unified environment utilizes ISO 10303 standard, newly developed for collaboration between electrical and mechanical software tooling. The standard was developed with the printed circuit board assembly enterprise in mind, where mechanical enclosures hold the PCAs for consumer or industrial use.
Take the worry and exasperation out of your design and development process. Get Altium Designer’s unified environment for complimentary use of 3D models across platforms. Use the Editor to define the 3D enclosure, along with placing your largest 3D components within the design for the definition of keepouts as the layout progresses.
If you’d like to know more, talk to an Altium expert today.