All About IPC-4101 and IPC-4103 Slash Sheets
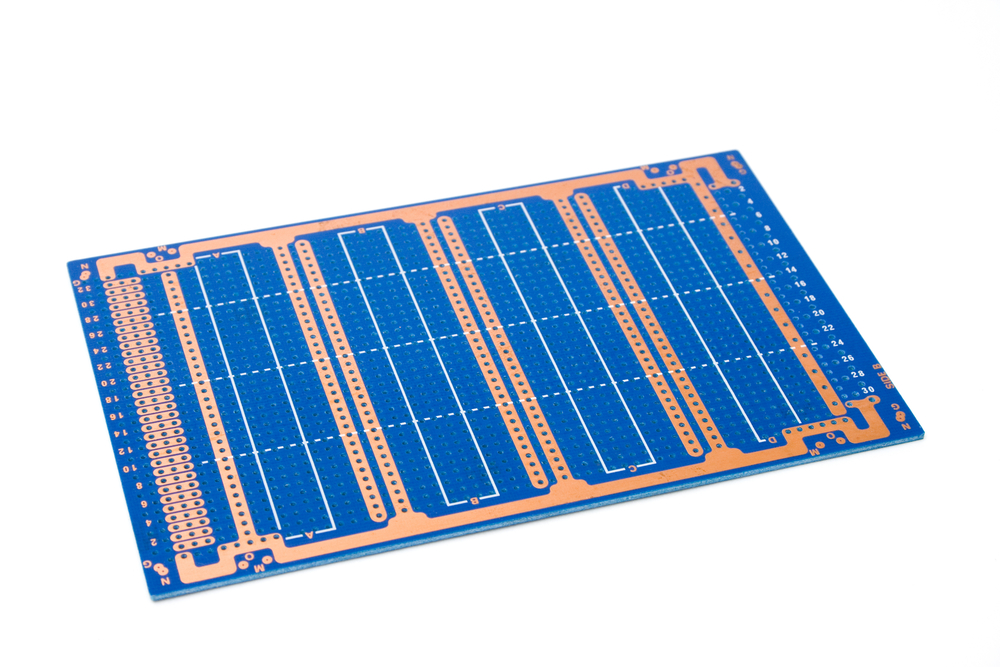
Before you do anything around planning a new PCB layout, the first thing you’ll need to do is design a stackup and select a material system for your board. PCB laminate materials might seem simple: you select a desired vendor and material from their catalogue, put these into your stackup, and you send it off to your fabricator, right?
The reality is that not all fabricators support or stock every possible laminate material, but some materials are compatible with each other in different stackups. How can you spot which materials and resin system will be interchangeable in your PCB stackup?
Enter IPC standards, specifically IPC-4101 and IPC-4103 slash sheets. Both standards specify various requirements for PCB laminate materials that help ensure interchangeability and compatibility in a PCB stackup. While you don’t need to read specific slash sheets when selecting materials, understanding what’s in a slash sheet can help you determine alternate materials if your desired laminates aren’t available or supported by your manufacturer.
The Origin of Slash Sheets
Under the IPC standards, specifically IPC-4101 and IPC-4103, slash sheets are addenda that state requirements for different classes of laminates for PCB stackups. The IPC-4101 standard used much of the original language from the MIL-S-13949 standard. The IPC originally stated that the 4101 standard makes MIL-S-13949 unnecessary, and this standard is now considered canceled as of December 1, 1998. IPC-4101 and related IPC-4103 slash sheet requirements persist to this date, and laminate manufacturers will list the slash sheets to which their materials conform.
If you look on a laminate manufacturer’s website or in their laminate datasheets, you’ll likely see a designation like “/121” or “/24” for specific laminates, which refers to the IPC-4101/121 or IPC-4101/24 slash sheet, respectively.
What’s in a Slash Sheet
Slash sheets contain two sets of data on a particular material system: primary structural/material properties and some testing results as determined under IPC testing standards. All slash sheets start with material and structural specifications for the particular laminate. Each manufacturer has their own material names they use to communicate specific laminates to customers and the public, but these laminates will be related to a specific slash sheet within the IPC-4101/IPC-4103 standards. The following information is included in a slash sheet:
- Reinforcement type (normally fiberglass)
- Resin material system (normally an epoxy mix)
- Any filler materials and flame retardants present in the laminate
- The glass transition temperature
This is the primary list of requirements a PCB laminate material needs to conform to in order to comply with the standards listed in the slash sheet. The rest of the slash sheet will list some characteristics the laminate must have as determined under the IPC-TM-650 Test Methods. These include:
- Peel strength, or the amount of stress required to separate two laminates after bonding
- Dielectric properties, including loss tangent, breakdown field strength, and surface resistivity
- Thermodynamic properties, including thermal resistance and moisture uptake rate
- Specifications for both prepreg and base material
Any material that claims to conform to one of the slash sheets in the IPC-4101/IPC-4103 standard must meet these standards. Note that subsection IPC-4101D is used for polyimide materials (/40, /41, and /42). Within the standard, the IPC specifies a list of permissible substitutions for various slash sheets (see the table below), which was finalized at a 2016 committee meeting.
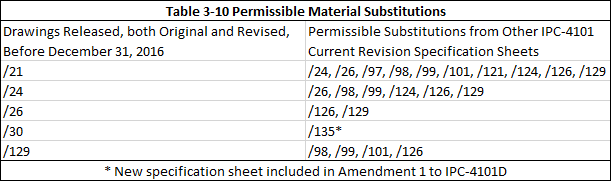
IPC-4101 vs. IPC-4103
You might see both standards mentioned when looking at a slash sheet from a laminate manufacturer. The IPC-4101 standard covers standard laminates and prepreg materials, encompassing epoxy resin materials with fiberglass. Although the standard originally specified 41 slash sheets, that number has grown to more than 60 slash sheets thanks to RoHS regulations and the focus on environmentally friendly lead-free materials. IPC-4103 extends slash sheets to copper-clad and unclad plastic laminate materials and bondply materials used in high-speed/high-frequency PCBs.
Plan and Calculate Your Stackup Early
If you’re like me, you have preferred manufacturers you like to use. Over time, when you keep ordering through the same manufacturer, you’ll become more familiar with their stackups and the list of specific materials they support. They’ll normally list this by laminate vendor name and number, rather than using the slash sheet number. However, some fab houses require you specify your desired stackup by slash sheet, so be sure to get this information from your laminate manufacturer when submitting your order, otherwise you might summarily annoy your fab house.
Preferred PCB Stackups
Many manufacturers have their “preferred” stackups they use for specific layer counts and that they can assure will pass through their fabrication process. These preferred stackups will include some specified material systems. You should check with your fabricator to make sure your idealized stackup is supported in their process. For example, radar modules will often use a hybrid stackup with a PTFE laminate on the outer layer for RF traces. If you’re planning to design one of these boards, make sure you’re designing to the preferred stackup that will support these materials and layer counts.
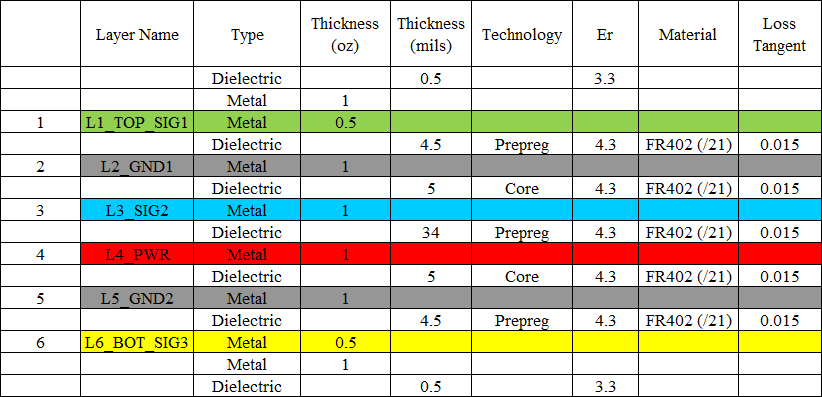
Not all manufacturers will place the slash sheet designation in a stackup table like this, but you can usually find the slash sheet designation on your manufacturer's website.
Where to Find Stackup Data
Some fabrication houses will put this online, others will send it to you in an email. Just make sure you ask early, otherwise you risk a complex redesign if you need to modify the stackup in a finished PCB layout, especially when the board is impedance controlled. If you’ve designed around one material system, but you’re forced to work under an alternative material, you can be reasonably assured the two materials will be equal substitutes if they are both designed to the same slash sheet. Just be sure to check the data sheets from both materials to make sure they are really compatible, and you might even consider ordering a test sample to check impedance and thermomechanical properties.
With the best PCB design tools in Altium Designer®, you can easily design any standard stackup based on your manufacturer’s data and slash sheets for your preferred laminate materials. You can also instantly create the fabrication files your manufacturer needs to fabricate your stackup and ensure accurate assembly.
When you’ve finished your design, and you want to release files to your manufacturer, the Altium 365™ platform makes it easy to collaborate and share your projects. We have only scratched the surface of what is possible to do with Altium Designer on Altium 365. You can check the product page for a more in-depth feature description or one of the On-Demand Webinars.