Reflexionen zum Thema Rigid-Flex – Teil 1
Immer mehr PCB-Designer sehen sich mit der Notwendigkeit konfrontiert, die Abmessungen und Kosten ihrer Produkte zu minimieren, indem sie die Bauteil- und Verbindungsdichte erhöhen und ihre Leiterplatten speziell für möglichst einfache Fertigungsverfahren auslegen. Eine gängige Option zur Bewältigung dieser Herausforderungen sind Rigid-Flex-PCBs – Leiterplatten mit zwei oder mehr starren Segmenten, die über flexible Lagen miteinander verbunden sind. Dieser Blogbeitrag trägt diesem Trend Rechnung. Er ist der erste Teil einer kurzen Serie über Rigid-Flex-Materialien, -Herstellungsverfahren und -Designmethoden.
Wie Sie dem Titel entnehmen können, habe ich in letzter Zeit viel über das Thema Rigid-Flex nachgedacht. Die vielen potenziellen Vorteile der Technologie haben mittlerweile das Interesse vieler Designer geweckt, die ihren Einsatz früher nicht erwogen hätten. Anscheinend bewirken die steigenden Anforderungen in puncto Bauteildichte und Fertigungszeit in Kombination mit dem starken Kostendruck ein Umdenken und veranlassen immer mehr Ingenieure und Designer zur Suche nach neuen Möglichkeiten.
Diese Entwicklung ist grundsätzlich begrüßenswert, birgt jedoch auch gewisse Risiken, da sich einige Aspekte der Rigid-Flex-Technologie als Fallstricke für Neulinge erweisen können. Daher möchte ich Ihnen hier die Möglichkeit geben, sich mit den Bestandteilen und den Fertigungsprozessen von Rigid-Flex-PCBs vertraut zu machen, bevor Sie Ihr erstes eigenes Design erstellen. Werfen wir also zunächst einen Blick auf die verschiedenen Materialkomponenten einer flexiblen Leiterplatte.
Materialkomponenten von Rigid-Flex-PCBs
Trägermaterialien und Coverlay-Folien
Konventionelle, starre Leiterplatten enthalten Trägerschichten aus Fiberglas und Epoxidharz. Interessanterweise handelt es sich hierbei um ein Gewebe, das tatsächlich ein gewisses Maß an Elastizität aufweist (was bei näherer Betrachtung von einzelnen Schicht aus diesem Material zu erkennen ist). Allerdings wird durch das ausgehärtete Epoxidharz sichergestellt, dass diese Lagen eine hohe Steifigkeit erreichen. Dadurch bekommen sie eine fest Struktur, die sich nicht für Anwendungsszenarien mit starker oder wiederkehrender Verformung eignet.
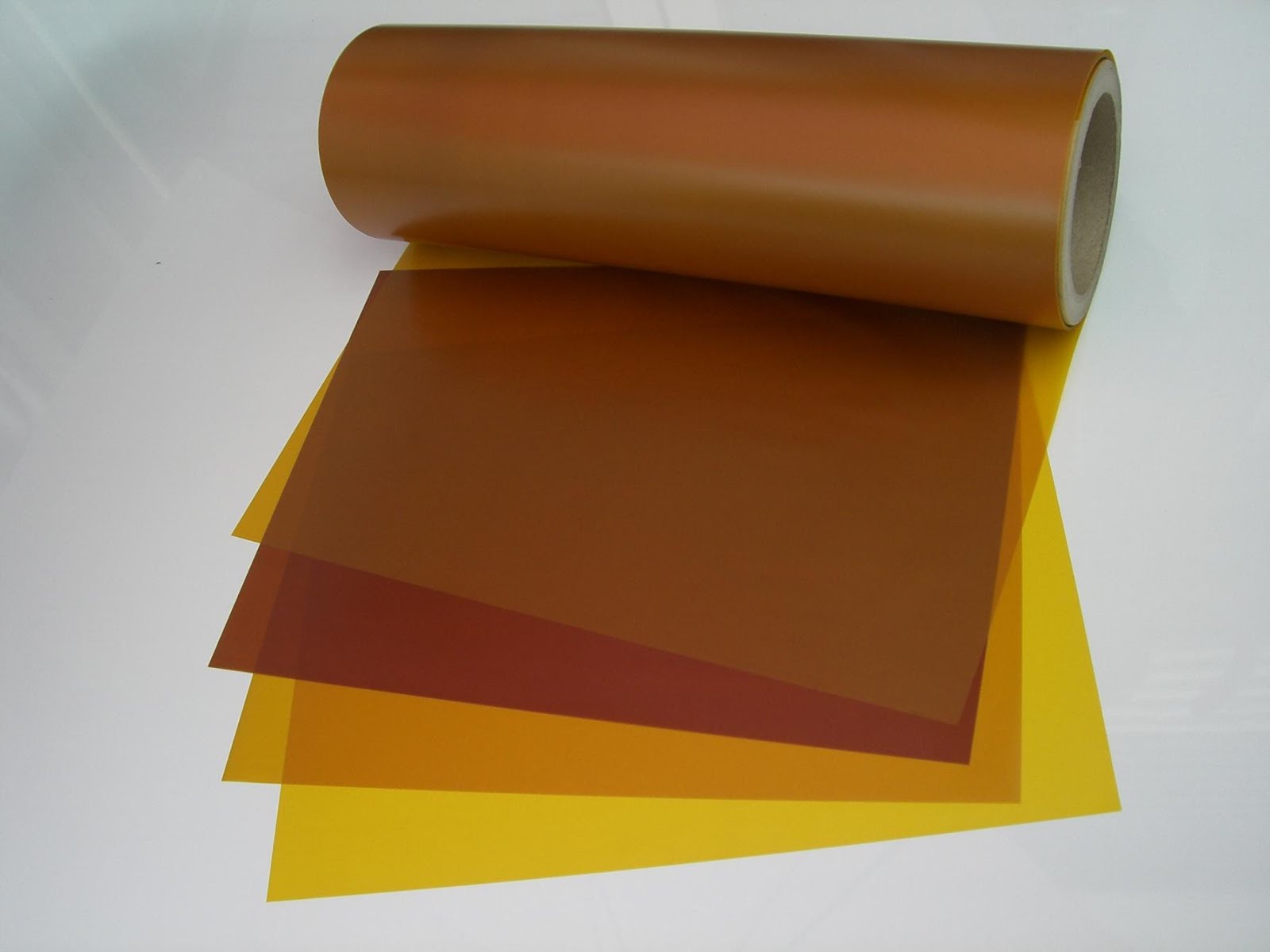
Für derartige Anwendungsszenarien ist meist ein Lagenaufbau erforderlich, der mehr flexible Plastikschichten und weniger Prepreg-Lagen umfasst. Das derzeit beliebteste flexible PCB-Material ist Polyimid (PI). PI-Folien sind nicht nur biegsam, sondern weisen auch eine hohe Widerstandsfähigkeit auf. Sie lassen sich von Hand nicht zerreißen oder strecken und überstehen daher problemlos sämtliche Schritte bei der Zusammenfügung der verschiedenen Lagen der Leiterplatte. Außerdem zeichnen sie sich durch eine extreme Hitzebeständigkeit und eine geringe Wärmeausdehnung aus, was unter anderem bedeutet, dass sie unempfindlich gegen Reflow-Zyklen und Temperaturschwankungen sind.
Ein weiteres gängiges Material für Rigid-Flex-PCBs ist Polyethylenterephthalat (PET). Allerdings sind PET-Folien weniger hitze- und formbeständig als PI-Folien und kommen oft bei der Produktion von Billigprodukten zum Einsatz. Da PET im Allgemeinen nicht robust genug für die gängigen Laminier- oder Lötverfahren ist, müssen die Leiterbahnen aufgedruckt und alle Kontakte durch bloßen Druck hergestellt werden. Ich selbst hatte beispielsweise einen Radiowecker, dessen Anzeige immer wieder ausfiel, weil die elektrischen Verbindungen der flexiblen, aus PET-Folie gefertigten PCB-Segmente so unzuverlässig waren. Daher möchte ich mich in meinen folgenden Ausführungen zur Rigid-Flex-Technologie auf PI-Folien beschränken. (Neben PI und PET sind weitere flexible Materialien verfügbar, die jedoch nicht oft verwendet werden.)
Die Liste der am häufigsten verwendeten Trägermaterialien für Rigid-Flex-PCBs umfasst also neben dünnen harzgetränkten Glasfasergeweben auch PI- und PET-Folien. Letztere kommen zusätzlich als Abdeckfolien (Coverlay) für die flexiblen Leiterplattenbereiche zum Einsatz und schützen in dieser Funktion die auf den Außenseiten verlaufenden Leiterbahnen vor Korrosion und Beschädigung – genau wie eine Lötstoppmaske ein starres PCB schützt. (Alternativ können zu diesem Zweck auch flexible Lötstopplacke verwendet werden.) Dabei liegt die Stärke der PI- und PET-Folien bei mindestens ⅓ und höchstens 3 mil, wobei Werte zwischen 1 und 2 mil typisch sind. Im Vergleich dazu sind die Prepreg-Schichten üblicherweise dicker und weisen Stärken zwischen 2 und 4 mil auf.
Materialien für Leiterbahnen
Auch wenn die Leiterbahnen der oben erwähnten Billiggeräte eventuell in Form einer Kohlenstoffschicht oder mit einer Tinte auf Silberbasis aufgedruckt sind, bestehen die meisten Leiterbahnen in flexiblen PCBs aus Kupfer. Je nach Anwendungsszenario bietet sich hier entweder der Einsatz von Elektrolytkupfer (ED-Kupfer) oder von geglühtem Walzkupfer (RA-Kupfer) an. Wenn die flexiblen Segmente Ihres PCBs nur der Minimierung der Zahl der Verbindungskabel und Steckverbinder und damit letztlich der Senkung der Fertigungszeiten und -kosten dienen, können Sie dieselbe laminierte ED-Kupferfolie nutzen, die auch bei der Produktion von starren Leiterplatten zum Zug kommt. Letzteres gilt auch für Fälle, in denen höhere Kupferstärken wünschenswert sind, damit die Leiterbahnbreite trotz hoher Stromstärken so gering wie möglich gehalten werden kann (beispielsweise zur Konstruktion einer Planarspule).
Zugleich ist zu beachten, dass ED-Kupfer geradezu berüchtigt für seine Tendenz zur Kaltverfestigung und Materialermüdung ist. Wenn Sie also ein Design für eine Leiterplatte erstellen, die wiederholt gebogen oder anderweitig verformt wird, sollten Sie unbedingt die höherwertigen RA-Kupferfolien in Erwägung ziehen. Diese sind einerseits erheblich teurer, weil ihr Herstellungsprozess den zusätzlichen Schritt des Auswalzens umfasst, bieten andererseits jedoch bessere Zugeigenschaften und eine höhere elastische Verformbarkeit entlang der Z-Achse – also genau die Qualitäten, die zur Vermeidung von Leiterbahnbrüchen in einem flexiblen PCB mit ständig wechselnder Biege- oder Rollverformung erforderlich sind. Dabei ergeben sich die verbesserten Werkstoffeigenschaften durch das horizontale Auseinanderziehen der Kornstruktur des Kupfers im Rahmen des Walzprozesses.
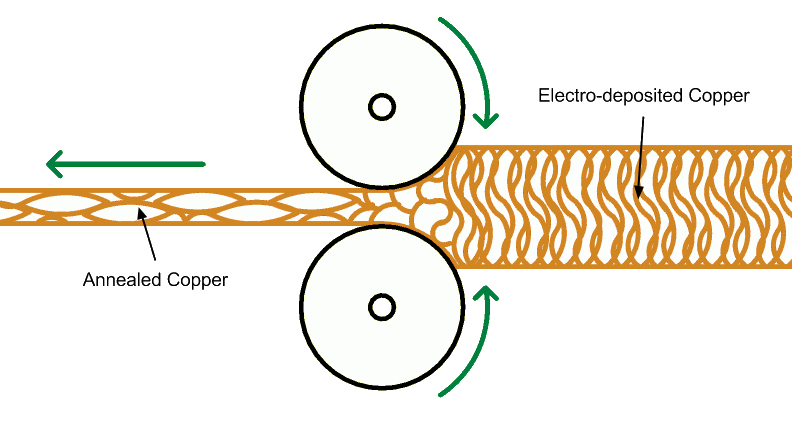
Abbildung 2: Nicht maßstabsgetreue Darstellung des Walzprozesses. Die Kupferfolie passiert eine Hochdruckwalze, die ihre Kornstruktur horizontal auseinanderzieht und so dafür sorgt, dass das Material insgesamt flexibler wird und sich in Richtung der Z-Achse besser elastisch verformen lässt.
RA-Kupfer wird unter anderem zur Fertigung von Flachkabelverbindungen für CNC-Fräsköpfe oder den Laser-Lesekopf eines Blu-Ray-Laufwerks (siehe unten) verwendet.
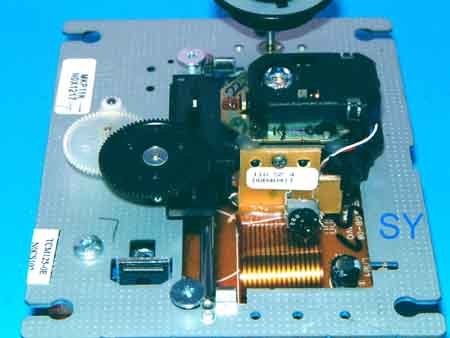
Abbildung 3: Flexible Verbindung zwischen Lesekopf und Mainboard eines Blu-Ray-Players. Hier ist zu beachten, dass die Flachkabelverbindung im rechten Winkel auf die Oberfläche des Laser-Lesekopfes trifft und dort eine scharfe Biegung aufweist. Zur Stabilisierung der Kontakte wurde diese Stelle mit einer Klebstoffschicht versehen.
Klebstoffe
Bei der Fertigung flexibler Leiterplatten wird die Kupferfolie üblicherweise auf die PI-Folie (oder ein anderes flexibles Trägermaterial) aufgeklebt. Dies ist nötig, da das RA-Kupfer weniger „Grip“ als das für konventionelle starre FR-4-PCBs gebräuchliche ED-Kupfer hat und sich durch Erhitzen und Verpressen nicht zuverlässig mit der Trägerschicht verbinden lässt. Hersteller wie DuPont bieten vorlaminierte, ein- und doppelseitig mit Kupfer beschichtete Folien an, auf die Leiterbahnen aufgeätzt werden können. Bei den hier verwendeten Klebstoffen handelt es sich um Epoxid- oder Acrylkleber, die in Stärken zwischen ½ und 1 mil aufgetragen werden und speziell im Hinblick auf größtmögliche Flexibilität entwickelt wurden.
Daneben finden mittlerweile auch klebstofflose Laminate immer stärkere Verbreitung, bei denen die PI-Folie unter Anwendung neuartiger Fertigungsverfahren entweder plattiert oder direkt mit Kupfer beschichtet wird. Diese Folien sind das Mittel der Wahl, wenn feinere Pitches und dünnere Durchkontaktierungen benötigt werden, was unter anderem bei der Realisierung von HDI-Designs der Fall ist.
Darüber hinaus spielen silikonbasierte Klebstoffe, Heißkleber und Epoxidharze eine wichtige Rolle bei der Stabilisierung von Rigid-Flex-Übergängen. Wenn die Schnittstellen, an denen die flexiblen Lagen aus einem starren Segment austreten, mithilfe von Klebstoffperlen mechanisch verstärkt werden, lassen sich Brüche und andere Ermüdungserscheinungen des Materials auch bei häufiger Beanspruchung verhindern. Dies ist exemplarisch in Abbildung 3 dargestellt.
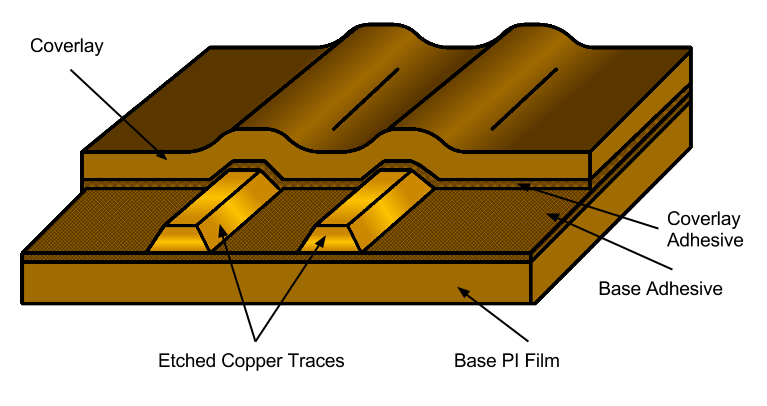
Abbildung 4: Typischer Aufbau eines flexiblen, einseitigen PCBs
Fazit
Es ist wichtig, über die verschiedenen Materialien für Flex- und Rigid-Flex-PCBs informiert zu sein. Wenn Sie bei der Auswahl der passenden Materialkomponenten für Ihre Anwendung stets blind auf die Empfehlungen Ihres Herstellers vertrauen, gehen Sie damit unter Umständen das Risiko ein, dass Ihr Endprodukt in der Praxis nicht die gewünschte Funktionalität bietet. Daher sollten Sie sich unbedingt ausführlicher über das Thema Rigid-Flex informieren und beispielsweise den einschlägigen Beitrag im „Printed Circuits Handbook“ (Coombs, C. F., 2008, 6th Ed. 2008 McGraw Hill, S. 61.3 0 - 61.24.) zurate ziehen.
Außerdem können Sie mit dem entsprechenden Wissen nicht nur den eigentlichen Designprozess, sondern auch die daran anschließende Evaluations- und Testphase straffen. Je besser Sie die verfügbaren Optionen und ihre spezifischen Vorteile kennen, desto leichter wird es Ihnen fallen, Ihre flexiblen oder starrflexiblen PCBs für widrige Umwelteinflüsse wie Hitze, Feuchtigkeit, ätzende Chemikalien und Stöße sowie den gewünschten minimalen Biegeradius auszulegen. Davon profitieren beispielsweise Designer aus der Automobilindustrie und Entwickler von vibrations-, sturz- und schweißresistenten Elektrogeräten für den Privatgebrauch.
Weitere Anregungen und Überlegungen, die bei der Erstellung von Rigid-Flex-Designs relevant sind, finden Sie im nächsten Beitrag aus dieser Reihe, in dem ich die verschiedenen Schritte der Herstellung flexibler PCBs erläutere.