新たなデジタルコラボレーションによってCalumet Electronics社にもたらされたプラスの影響
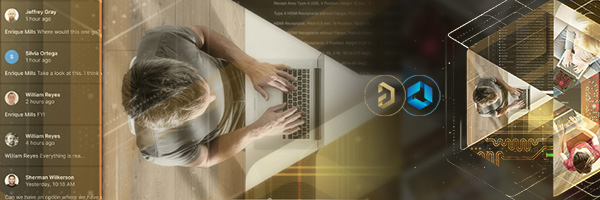
Judy Warner: Robさん、Calumet Electronics社とご自身の担当業務について簡単に教えてください。
Rob Cooke: Calumet Electronicsには、エンジニアリングサービス担当責任者として1年半ほど勤務していて、新しい注文を処理するCAM/工具グループを担当しています。また、設計エンジニアリングサービスグループとソフトウェア開発チームも管理しています。Calumet Electronicsは、1968年から米国でプリント基板を製造している設立50年以上の企業です。当社の使命は、安心かつ安全でサステナブルな回路基板製造業者であることです。
Warner: 短期間でプリント基板を製造するうえでの大きな障害は、設計者が製造業者にデータファイルを引き渡した後に生じる情報断絶です。作業の開始にあたって必要になる重要な情報が不足しているために、保留される作業はどれぐらいあるでしょうか?また、Calumet Electronicsとお客様にはどのような影響があるでしょう?
Cooke: ある基板業者のCEOは、情報不足のため保留される作業は「全部」だと言っていました。私の経験に照らしても、この意見はかなり的を射ていると思います。基板にも製造にもさまざまな選択肢があるため、図面、発注書、仕様書だけですべてを網羅することはできません。図面や設計パッケージは、設計の詳細を伝えるための1つの手段にすぎません。設計の意図がすべて伝達されて完全に理解されるかどうかは、関係者間のやりとりにかかっています。
Warner: 不足することが多い情報はどのようなものでしょうか?設計者は何に留意する必要があるでしょう?
Cooke: 非常にたくさんあります。最も一般的で単純なケースとしては、製造にとって重要なアートワークファイルとドリルファイルを設計者や調達担当者が渡し忘れることです。ですが、多くの問題はもっと把握しにくいです。たとえば、ネットリストファイルに意図的な短絡や開回路が含まれていても、それを伝えてくれないことがあります。また、インピーダンスをコントロールした配線が含まれている場合は、どのラインがそれに該当するかわからなければ問題です。相反する、あるいは最新技術では実現できない間隔やアニュラリングの制約については、コールアウトを追加することが一般的です。多くの場合、IPC 6012のクラス2またはクラス3の仕様は、特定の最小許容差の制約を意識せずにコールアウトが追加されますが、提供された設計ではその制約を満たすことができません。
Warner: 先日、「Altium 365の推薦をご希望でしたらお知らせください。私は熱狂的支持者ですので!」とのメールをいただきましたが、なぜそのようなメッセージをくださったのでしょうか。
Cooke: このツールを使ってみて、今のデジタル時代にコミュニケーションとコラボレーションがどのように功を奏するかをほぼ完璧に体験できたと感じたからです。基板の製造が必要な設計者と仕事をしていたときのことです。その設計者が基板製造についてのオンライン会議を招集し、アセンブリ業者にも参加するよう求めました。その時点で、設計はおよそ85~90%完成していました。設計者から提示されたのは5つの基板設計でしたが、Altium 365を使ってそれぞれを詳しく見ていきました。アセンブリ業者と私は基板レイアウトを確認しながら、基板のスタックアップからコンポーネントのはみ出し、パレットのスペース設定や基準に至るまで、製造に関して問題が発生しそうな箇所を洗い出しました。マーキング、ソルダ―マスク、穴の許容差などに関してよく発生する疑問点についても、製造図を仕上げる前に話し合いました。サプライヤーの選択は設計者側の仕事でしたが、そのおかげで基板用の工具を1日足らずで準備できました。製品に使用する5枚すべての基板のレビューは、3日間で完了しました。致命的な情報不足で何週間も足止めされるのとは大違いです。
Warner: 他の仕事も同じように順調に進められれば、RobさんやRobさんのお客様にとって何が変わるでしょうか。
Cooke: 最大のメリットは、製品化に要する時間が増えることとリスクが削減されることです。私の経験では、基板が完成するのに1~2週間待ったあげくに、製造上の問題のために基板が廃棄されることほど大きなストレスはありません。問題の多くは、事前にほんの少し話し合ったり分析したりすれば回避できるのです。確かに、自動化されたDFMツールやデザインルールチェックはとても便利ですが、製造に引き渡す前に製造業者やアセンブリ業者の代わりに設計をチェックすることはできません。先ほどの5つの設計のケースでは、製造やアセンブリに関するすべての疑問点について、30分未満で設計ファイルで調べることができました。早い段階で、すぐに変更できるクラウドベースのプラットフォームで共同作業したからこそ実現したことです。
Warner: 読者である設計者の方々に、製造へのスムーズな移行に役立つアドバイスをお願いします。また、電子ハードウェアの設計から完成までに、Altium 365がどのような影響を与えると思われますか?
Cooke: 基板設計にキャリアの大半を費やしてきた設計者として、Altium 365で強力なコラボレーションが実現すると考えています。視覚的なコンテキストを備えたコラボレーション環境で設計者とサプライチェーンのパートナーが連携できれば、膨大な時間と費用が節約されます。基板製造業者が設計ツールから直接レイアウトを共有して確認できるAltium 365を使用すれば、設計者は他の技術者の専門知識を活用することができます。場合によっては、何を優先するかがリードタイムに大きく影響することがあります。たとえば、材料の厚さや種類を少し変更するだけで、在庫数に応じてリードタイムを2~3週間節約できることもあります。見積もり前に設計を確認して提案を出せれば、大きな違いが生まれます。
Warner: 最後になりますが、何か他に思われることがあれば教えてください。
Cooke: 製造業者が直面する課題を取り上げていただいてありがとうございました。すべての基板はそれぞれに違います。大量生産される製品ではありません。今日の技術は、機械と人間の能力の限界を押し広げます。当社は現在、25ミクロン未満でトレースを配置する技術に取り組んでいます。また、設計者が順調に仕事を進められるよう支援したいとも考えています。共有できる情報や専門知識を十分に活用できなければ、限界を超えることはできません。Altium 365プラットフォームは、物理的な場所に関係なくこうしたコラボレーションを促進し、すべての関係者のギャップを埋めてくれる最新のソリューションです。設計技術者や製造業者にとって、感動的なツールです。
編集者メモ: このテーマに関するRob Cooke氏へのインタビューは、 OnTrackポッドキャストでも視聴できます。
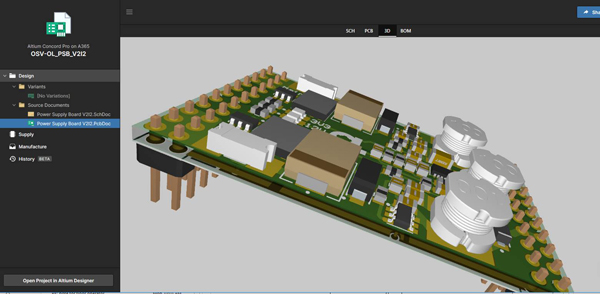
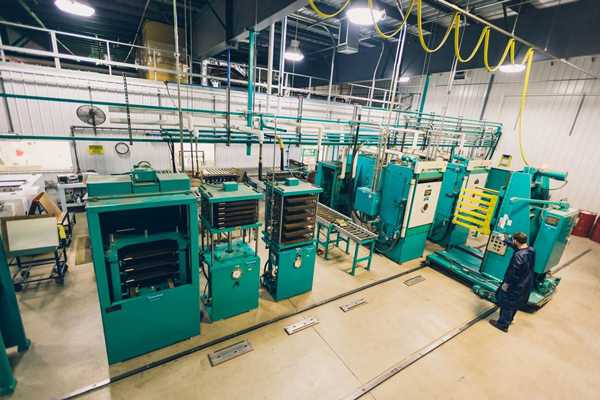
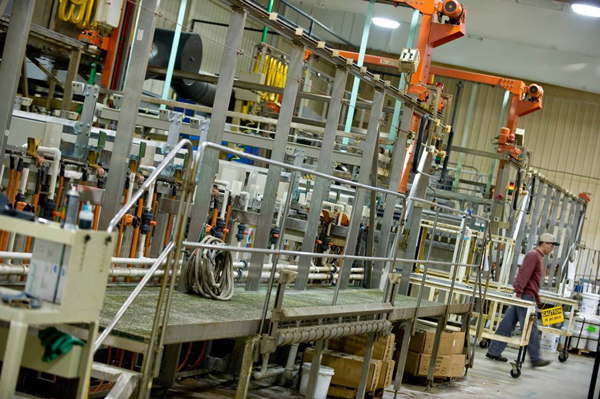
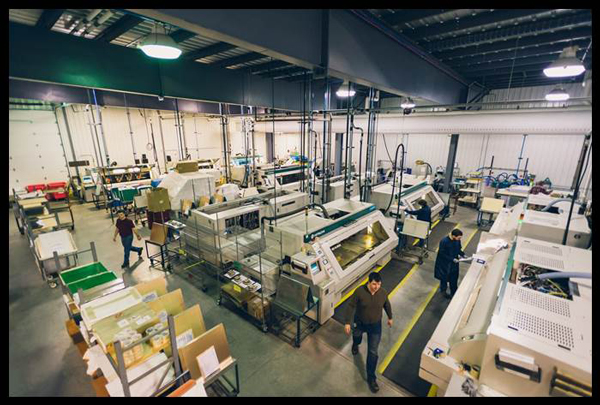