Suggerimenti per ridurre il costo di un PCB
Saper ridurre i costi di produzione di un PCB è considerata una skill fondamentale al giorno d’oggi data la forte pressione del mercato sui prodotti elettronici, specialmente nel mondo consumer e high volume. In questo articolo verranno illustrati alcuni accorgimenti e regole generali per abbassare il costo di produzione di una scheda elettronica. Prima però cercheremo di capire quali sono i fattori che hanno influenza sul costo del PCB.
Fattori che determinano il costo di un PCB
Gli elementi principali che stabiliscono il prezzo di un PCB possono essere raggruppati in tre categorie:
- I costi di materiale, ossia il costo del materiale che deve essere acquistato per produrre un PCB. Tale costo è dato dalla somma dei prezzi di tutti i componenti della board (BOM) ed il costo del PCB stesso.
- I costi di assemblaggio, ossia quanto costa posizionare tutti i componenti sul PCB ed effettuarne la saldatura.
- I costi di testing, ossia quanto costa validare un PCB assemblato verificandone tutte le sue funzionalità.
Per ottimizzare questi costi il progettista può usare accorgimenti in tutte e tre fasi di progettazione principali del flusso di design PCB: schematico, layout e testing. Vediamo per ognuna di esse quali sono le ottimizzazioni applicabili.
Ottimizzazioni in fase di schematico
La principale ottimizzazione a livello di progettazione schematico che ha un impatto fondamentale sui costi di BOM e di assemblaggio è quella di ridurre il numero totale di componenti diversi sulla board. Un esempio semplice potrebbe essere quello di sostituire una resistenza da 200k con due da 100k in serie già utilizzate in altre parti dello schematico, oppure unificare i componenti discreti come diodi o transistor usando sempre lo stesso componente se elettricamente compatibile.
Molto spesso i valori di resistenze a capacità vengono estrapolati da formule presenti sui datasheet o application notes di circuiti integrati utilizzati sui PCB. Potrebbe valer la pena valutare l’impatto dell’utilizzo di un valore non esattamente coincidente con quello stimato dalla formula ma già utilizzato in qualche altra sezione del design. Spesso, e meno di circuiti usati per genere riferimenti precisi, la sostituzione è possibile; specialmente se si pensa che la capacità utilizzate comunemente possono avere una tolleranza tra il 10% ed il 20%.
Ridurre tale numero ha un effetto benefico sul costo della BOM, si deve infatti tenere presente che i costi di acquisto di un componente si abbassa con il volume di acquisto del componente stesso. Consolidare la BOM significa aumentare i volumi totali di componenti più usati ed eliminare componenti con bassi volumi dalla BOM.
Ridurre i tipi diversi di compenti del PCB ha anche un grosso beneficio sui costi di assemblaggio, i quali sono proporzionali al numero di macchinari Pick and Place usati sulla linea di assemblaggio ed al tempo necessario per assemblare una scheda. Infatti, i macchinari Pick and Place sono equipaggiati con un numero limitato di slot per i reel dei componenti, ed ogni tipo diverso di componente occupa uno (o più) di questi slot. Quindi ridurre il numero di tipi diversi di componenti riduce il numero potenziale di macchinari Pick and Place necessari sulla linea di assemblaggio.
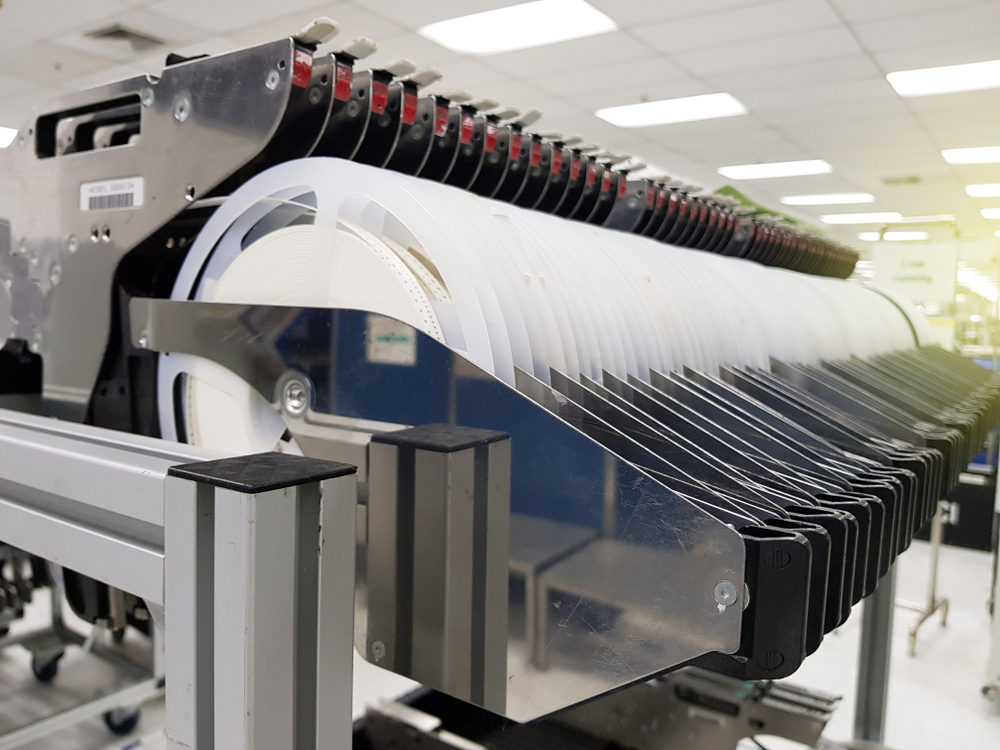
Ottimizzazioni in fase di layout
Utilizzare il più possibile componenti con lo stesso footprint può comportare un ulteriore riduzione dei costi in fase di assemblaggio. Infatti, le testine (head) usate nelle Pick and Place machine possono essere custom per specifici package SMD (0201, 0402 etc…). Se nel design in questione vengono utilizzati per esempio solo resistenze e capacità 0402 questo comporterà l’utilizzo di un unico tipo di testina con relativo abbassamento del costo di assemblaggio.
In generale ridurre il numero di footprint diversi utilizzati offre anche una maggior flessibilità in fase di ottimizzazione BOM aprendo la possibilità di sostituire i componenti con alternative meno costose pur mantenendone la compatibilità in fase di assemblaggio.
Un’altra ottimizzazione in fase di layout consiste nel ridurre il più possibile il numero di componenti thrugh hole. Valutare se possibile utilizzare solo componenti SMD, eliminando completamente la fase di saldatura thrugh hole che, a seconda del volume di produzione, potrebbe anche essere effettuata a mano.
Per quanto riguarda il PCB stesso ci sono vari fattori che concorrono a determinarne il prezzo e sul quali il progettista può agire:
- Dimensioni del PCB, evitare forme non rettangolari se possibile in quanto le parti di pannello non utilizzate sono comunque contabilizzate nel costo del PCB.
- Scegliere il materiale opportuno per il PCB con coefficiente termico appropriato per l’applicazione.
- Qualora nel design fossero presenti tracce ad impedenza controllata valutare se è possibile realizzarle usando lo stack up di default del produttore del PCB e utilizzando FR-4 come materiale di substrato. L’alternativa è quella di passare a materiali con costante dielettrica controllata ma di conseguenza molto più costosi.
- Scegliere la finitura opportuna per il PCB tenendo presente che la finitura (HASL) Hot Air Solder Leveling è generalmente quella meno costosa.
- Consolidare le diverse dimensioni dei fori sul PCB. Per ogni tipologia di foro diversa la drilling machine dovrà selezionare una punta diversa aumentando il tempo necessario forare tutta la board.
- Utilizzare laminati con spessore di rame superiore a 1oz solo se necessario per dissipare potenza o per requisiti di current capability.
Ottimizzazioni in fase di testing
Una volta assemblato il PCB esso dovrà essere testato per verificarne tutte le sue funzionalità e garantire un alta qualità del prodotto. Per effettuare questo test spesso il PCB viene inserito da un operatore all’interno di una fixture di test e vengono eseguite delle operazioni che possono essere automatizzate o meno. In generale il costo della fase di testing è direttamente proporzionale alla durata del test stesso e inversamente proporzionale al grado di automatizzazione. Diviene quindi fondamentale realizzare una test fixture in grado di testare il PCB nella maniera più rapida ed automatizzata possibile. Per far ciò il PCB stesso potrebbe essere equipaggiato con componenti per facilitarne il test come test points, connettori di debug o algoritmi embedded di self testing (BIST).
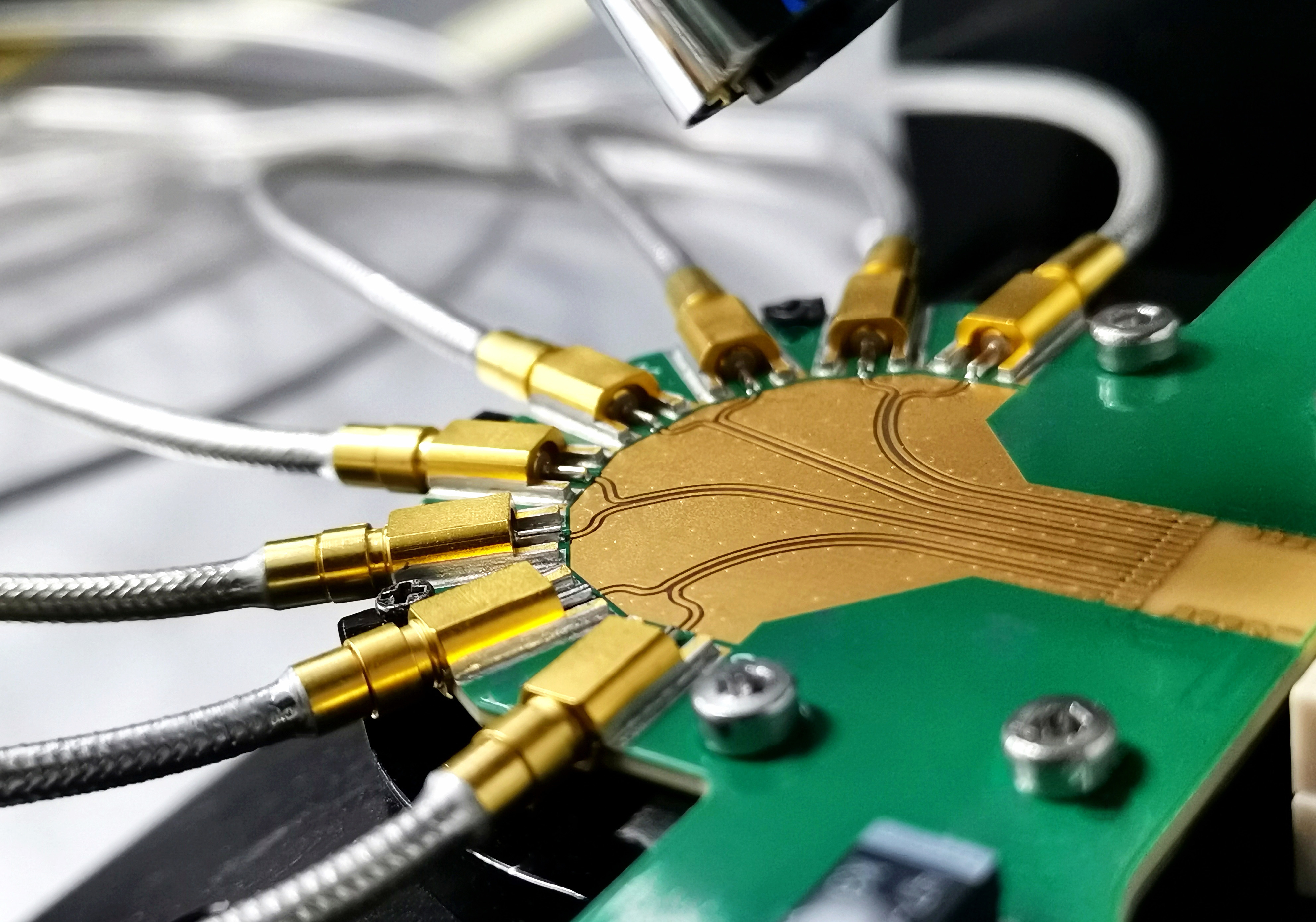